Screw Shaft Manufacturer Takes Flight with Kerf
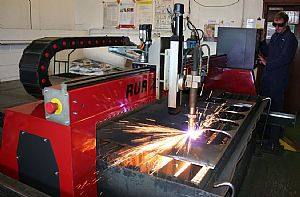
When Pressed Flights started business as a two man company producing garden gates, railings and bespoke designs for general industry and local councils almost 25 years ago, the company had little realisation that it would one day become a market leader and international supplier of screw flights, screw shafts, bucket elevators, screw conveyors and feeders.
Wind forward quarter of a century and the Littleborough company has invested in the latest CAD/CAM facilities and machine tools to cement its leading position in its niche market. The latest addition to the Lancashire company's plant list is a new Kerf RUR2500P plasma cutting machine for cutting its screw profiles. The screw profiles from 50mm to 4m diameter are machined on the Kerf RUR 2500P prior to being pressed to a form that is then assembled and welded around a turned bar to create a thread profile.
The company has gradually progressed from producing small screw flights to delivering larger projects that involve the mixing of anything from chocolate and crisps for some of the UK's household food manufacturers to the mixing of products for the pharmaceutical, food, cement, distillery, cattle feed, water treatment, chemical, recycling, mining, brewing and quarrying industries. Producing screw flights and shafts for all industry sectors requires Pressed Flights to manufacture from a host of materials that include brass, aluminium and stainless steel through to more difficult materials such as hardox, duplex, titanium and hastelloy.
Whist the machine shop with its turning and milling centres can comfortably adapt to the bespoke nature of the workload, the processing speed in the profile cutting department was restricting the production flow prior to the arrival of the Kerf RUR2500P. As Pressed Flights General Manager, Mr Mark Cryer comments: "We previously had a small conventional plasma cutting system for our production runs. This was limited to cutting material up to 12mm thick, so our workload was restricted by the machine's capabilities. The plasma cutting bottleneck was delaying our delivery lead times and holding our business back."
However, the arrival of the Kerf RUR2500P changed all this as soon as it was delivered. "From the outset, the Kerf RUR2500P machine significantly increased our productivity by over 2.5 times. What we used to produce in 5 days is now possible in 2 days. With such an increase in productivity, our lead times have tumbled and our capacity has more than doubled. The Kerf machine immediately eradicated any bottlenecks and our turnover has increased as a result of acquiring the machine."
Whilst eliminating bottlenecks was a key feature for Pressed Flights, the company soon witnessed a number of additional benefits to buying the Kerf machine. Firstly, the RUR2500P can cut materials up to 35mm. This increased the company's ability to produce larger screw flights with thicker materials for robust applications that were previously beyond the company's scope with the previous 12mm capacity machine. Secondly, the previous conventional plasma machine was a 45amp unit whilst the RUR2500P has significantly more power with a 150amp output. This enables Pressed Flights to cut difficult materials such as duplex and nickel alloys as fast as it would cut brass or aluminium whilst minimising dross.
The elimination of dross is credit to the 'ultrasharp' technology that is intuitively controlled by the Burny CNC control that is standard on the RUR Series. The Burny control fully automates the process to provide remarkable ease of use for the customer. To simplify operation, the Burny CNC utilises Inova arc voltage control and advanced command messaging to minimise divots and drag when processing the material. Additionally, the Burny control system includes nesting software that assigns tailored lead-ins and lead-outs for each individual component to improve part quality, a feature Pressed Flights has witnessed the potential of.
The previous conventional system would be significantly slower when cutting difficult materials whilst the dross remaining on the parts would require manual removal. This manual task would take an employee up to three days a week, a considerable labour requirement for the 14 employee business. The Kerf RUR2500P with its Kaliburn high definition system provides clean cuts with impeccable edge finishes that require no secondary cleaning operations. Whilst the RUR2500P has eliminated secondary finishing and the respective hand finishing processes as well as improving component quality; the innovative new plasma system has also reduced costs for Pressed Flights.
Highlighting the savings, Mr Cryer continues: "Whilst the consumables such as the torch parts, electrodes and nozzles required changing up to four times a day with the previous system, the RUR2500P consumables only need changing around once a day. Additionally, the Kerf machine is fitted with a 'fast disconnect' system. Whereby the previous machine would take over 5 minutes to change the parts up to 4 times a day, the Kerf machine allows us to pre-load new torch bodies so changeovers are done in 5-6 seconds. This saves us a couple of hours in downtime each week.
In conclusion, Mr Cryer comments: "The Kerf RUR2500P is a robust machine that is manufactured to deliver precision with minimal maintenance requirement. Moreover, the quality of our components has improved significantly, as has the consistency of the screw flights produced on the plasma machine. We are delighted we acquired this machine as the quality and consistency is supported by service support that is first class."