Seeing clearly with SINJIN Contact Lenses
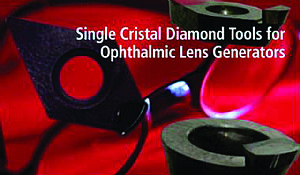
Ultra-precise diamond tools from the Korean company SINJIN give shape to lenses for glasses and contact lenses. For the production of its diamond-tipped profile cutters, the company is relying upon the precision of the Vollmer QXD 200 eroding machine.
The profile cutters are mainly used to machine glass or plastic lenses for glasses. Ophthalmology – has an everyday relevance for around half of the world's population that require treatment for diseases of the eye. The best-known aspects of ophthalmology are vision aids, such as glasses and contact lenses, made from glass or plastic.
The two Germans Adolf Eugen Fick and August Müller independently created the first glass contact lenses around 1880. However, contact lenses only really made a breakthrough in the mid-20th century, once high-quality synthetics such as acrylic glass could be used to produce them. Today, most lenses in glasses are made from high-quality synthetics. Regardless of whether glass or plastic is used, a decisive factor in ophthalmology is how the lenses of glasses and contact lenses are processed. The more precisely they are ground, the sharper the vision. It has now been a long time since lenses were ground by hand. Instead, ultra-modern CNC-controlled diamond tools are used, like those developed by the South Korean company SINJIN Diamond.
"When grinding the lenses of glasses, and even more so in the case of contact lenses, precision as accurate as a few microns is required. To enable this, we produce tools from natural and synthetic mono-crystalline diamonds, with tips just a few microns in size," explains In Sun Cha, President of SINJIN Diamond.
The medium-sized company was founded in Seoul more than 35 years ago, and now employs 20 people. In the global market for ultra-precise diamond tools,
SINJIN Diamond is one of the technology leaders, with a market share of around 30%. Particularly in the case of diamond tools with 'controlled waviness', SINJIN Diamond is one of just a few providers worldwide. Waviness is an undesirable side effect of machining surfaces with rotating tools. The waviness denotes the deviation from the norm, or how much the actual product deviates from the drawn plan. This deviation should be as small as possible. Machine tools with 'controlled waviness' monitor this deviation from the norm during machining, thus guaranteeing previously defined error tolerances.
"We supply diamond tools with a controlled waviness of less than 50 nanometres. Both insert systems and monobloc systems are available," adds In Sun Cha. "We deliver these ultra-precise diamond tools throughout the world. They are not only used for contact lenses, but also for the production of cameras, telescopes, and laser printers."
Lenses and mirrors for cameras and telescopes can have a diameter of 20 centimetres or more. These too are developed using the technology and knowledge of SINJIN Diamond. And every single laser printer works only thanks to the use of diamond tools! They are used to grind polygon mirrors that deflect the laser light inside the laser printer and light the image cylinder for printing.
"In an increasing number of technical applications, the force of the diamond dictates the level of quality and functionality," says In Sun Cha. "For this reason, we sought out a Vollmer sharpening machine for machining diamonds. It allows us to reach the level of precision that our customers expect from our products."
With the Vollmer QXD200 eroding machine, SINJIN Diamond manufactures diamond-tipped profile cutters that are primarily used to machine glass or plastic lenses for glasses. Thanks to the eroding machine, a profile cutter can be fully sharpened with a surface roughness of less than one micron in four to five hours. The Vollmer machine achieves this high precision because it measures, erodes, grinds and polishes the edges of the diamond-tipped milling tool in a single clamping. This full machining is based on six CNC axes that control the eroding process and make manual intervention superfluous.
"An integrated tool changer and comprehensive workpiece guidance mean that we can use the QXD200 to machine our profile cutters without manpower all day long – that's a good 40 tools per week!" explains In Sun Cha.