Stepping Into 5-Axis Machining With Open Mind
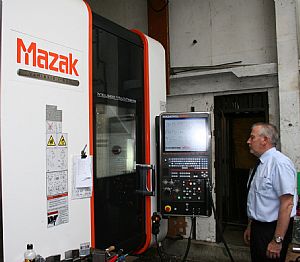
When Copsey Engineering committed to set itself as a benchmark in the subcontracting industry, the Essex manufacturer made its first step from 3 to 5-axis machining with the acquisition of an OKK 5-axis machining centre and CAM software from OPEN MIND Technologies to drive the business forward.
Since acquiring the OKK VP600 machine and its first seat of hyperMILL in 2006, the company has since invested over £1.2m in machine tools with the inclusion of three Mazak 5-axis machines and an additional three seats of hyperMILL to support the machine purchases. As Copsey Engineering, Managing Director, Mr Stephen Collins comments: "We didn't want to be a 'Fred in the Shed' subcontractor, so we invested in the best available machine tools and CAM software. From a CAM perspective, we investigated the market and noted the amount of marquee OEMs using hyperMILL. Our investigations led to demo's from five leading vendors and we instantly noted why the blue-chip OEM's use hyperMILL."
The learning curve for full 5-axis machining was followed by the onset of the 2008 recession that limited the available 5-axis workflow. During the downturn, the company won a defense contract to manufacture 30,000 steel axles and hubs. Processing over 30 ton of material each week for 9 months, the company comfortably saw its way through the downturn. Since the recession, the Witham company has flourished with its increased 5-axis capabilities. The ensuing success is what brought an influx of Mazak 5-axis machines & hyperMILL seats over the last 2 years.
Exceeding the remarkable business levels achieved during the downturn, 27 employee Copsey Engineering runs its machine shop 24 hours a day and six days a week. Supplying small infrequent batch runs, the irregular schedule of parts of varying complexity would create bottlenecks and scheduling issues for most manufacturers. However, at Copsey, additional hyperMILL seats were acquired to enable shop floor machinists to generate their own component programs at the side of the machine tools. As Mr Collins continues: “With our through flow of complex parts, one programmer on hyperMILL wouldn’t have been sufficient. Instead of one programmer trying to impossibly program 10 jobs, we now have four guys doing 2-3 jobs each, so no machine lies idle waiting for a program to be generated.”
Since employing hyperMILL and the 5-axis Mazak machine tools, turnover for the aerospace, defense, marine, automotive, broadcasting, medical and agricultural subcontractor has grown by over 30% whilst profit margins have drastically improved. This is credit to hyperMILL being utilised for 3-axis as well as 5-axis components. As Mr Collins states: “Our 3-axis Mazak machines have always been programmed using the Mazatrol control on the machines. By programming even 3-axis parts with hyperMILL we have reduced lead times and increased profit margins by over 60%.”
To demonstrate this, Mr Collins refers to a long term job the company has been producing for over nine years; “We have one job that requires holes in all sides and multiple set-ups. Unfortunately there hadn’t been a price increase on the combined electrical boxes for nine years and it was becoming unprofitable. By moving the complex job from a 3 to 5-axis machine, we reduced the lead time of a batch of 100 from 3 days to 4 hours. This improved our capacity and more than doubled the profit margin on this job.” Whilst the customer was still enjoying a 9 year old price.
The company is more than happy with its decision to purchase hyperMILL, confident that it can produce any job that comes through the door. As Mr Collins says: “With hyperMILL we have the confidence to tackle any job, in this respect we have expanded the scope of our work and brought in more complex and more profitable work from a wider range of prestigious industry sectors.”
With regard to flexibility, hyperMILL has been a revelation for Copsey Engineering. Running a multitude of 3 and 5-axis machines, OPEN MIND has provided post-processors for all machines. The benefit is that all jobs only need to be programmed with hyperMILL once and can then be transferred from one machine to the next. If one particular machine is already in production, a job can be moved to an alternate machine. This flexibility afforded by hyperMILL enables the company to be less rigid with its planning and scheduling of jobs.
Discussing this situation, Copsey Engineering’s Works Manager, Mr Mick Brown says: “The flexibility from OPEN MIND’s post-processors have been a major boost to the through-flow and scheduling of our workload. However, as someone using hyperMILL daily, it’s the speed the CAM software gets us through programming to final part that is a real time saver. hyperMILL allows us to incorporate vices and workholding devices into the program, so we can visualize awkward jobs on the screen and ensure our toolpaths and set-ups are correct. If we ever make errors, hyperMILL’s collision avoidance feature is second to none.”
Other features the Works Manager likes within hyperMILL are the hole feature recognition that intuitively works through the model and laying out features. Whereas the profiling application enables the programmer to locate where the tools should be in relation to surfaces, simplifying complex shape production. Another feature that is a major plus for Copsey Engineering is hyperMILL’s mirroring function. The ability to program a right/left hand part and allow hyperMILL to quickly re-calculate the program for the opposite hand regularly saves the drawing office hours of programming time each week.
As Mr Brown continues: “We have been manufacturing camera tripods for the broadcasting industry for years. With a number of left and right hand parts, programming times have been drastically cut. From a productivity perspective, we used to machine tripod heads on the lathe and then machining centre in over 45 minutes. By optimizing our toolpaths in hyperMILL we have cut the time to 20 minutes.”
“The arrival of OPEN MIND’s hyperMILL CAM package has improved our cycle times and productivity, increased our capacity and also delivered complete flexibility for work scheduling whilst reducing on-machine programming times. Away from the shop floor, it has proven easy to use and intuitive and has allowed us to target more complex work from a wider range of industry sectors. This is a major factor in our ongoing growth and upturn in our turnover and profit margins. We picked OPEN MIND based on the recommendations of leading OEMs and we haven’t been disappointed. It’s delivered everything we wanted and much more,” concludes Mr Brown.