Subcontractor Buys Hi-Spec Tornos Based on YouTube Footage
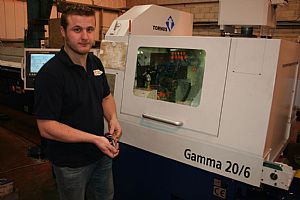
Starting a machine shop at the age of 24, in the run up to a recession undoubtedly shows the desire of Hi-Spec Engineering Ltd's Director Mr Darren Grainger to run his own business. However, renting a unit, buying his first three manual machine tools for a total of £3,500 and building the business whilst working a full time post at another company shows the maturity and determination to succeed.
Now, Darren has taken Hi-Spec to a company with 10 employees and a plant list that includes Haas and Hurco CNC machining centres and Colchester turning centres. However, Mr Grainger is keen to keep abreast of technology to build his business further. So, it was very apt that when Hi-Spec needed a new CNC turning centre, the decision was based primarily on video footage watched on video streaming website YouTube.
As Mr Grainger recalls: "We had an increasing demand for smaller diameter work that our existing CNC turning centres were not geared for. Additionally, we were having reliability issues, so the acquisition of a new and smaller turning centre would cater for the new work and ease the load on less reliable machines whilst improving lead times. We knew MACH 2012 was around the corner, but couldn't afford to take more than a day at the show investigating the available machines. I started to investigate all the leading machine tool suppliers on-line and watched numerous video footage. It was the footage of a Tornos Gamma on YouTube that took me straight to their stand at MACH 2012. I was given a demo to confirm that it could do everything I had seen in the YouTube video and I shook hands on it with Tornos on the very first day of the show"
Six months down the line and Mr Grainger is not only delighted with the acquisition, but can also confirm why he opted for the Tornos as opposed to an alternate sliding head centre: "From the YouTube footage we could see the Gamma 20 would be well suited to our small parts. When we investigated further and compared to competitor machines we identified a number of aspects that made the Gamma a better buy."
"Firstly, the Gamma 20 had high pressure coolant as a built-in unit whereas alternate machines only offered this as a bulky add-on feature. Secondly, the Tornos was the only machine to offer a guide-bushless system for working closer to the headstock. This delivers improved rigidity and flexibility as well as the ability to reduce bar remnants by up to 20%, which is considerable with the increasing material costs. Furthermore, the Gamma 20 also offered more tooling positions and more driven head tooling stations as standard. All this made the Tornos a more cost effective and attractive solution for us, a company taking its first step into the sliding head market," says Mr Grainger.
As a manufacturer of components and assemblies for the hydraulics, automotive and agricultural industries, producing valves, fittings, cylinders, power packs and drive couplings, the daily work schedule at Rutland based Hi-Spec can entail small to large batch sizes from a variety of material types. With batches that can range from 10 to 2000 in the turned parts department, the Tornos has slotted into the production flow perfectly at Hi-Spec. As Mr Grainger states: "As soon as we transferred parts from our fixed head CNC turning centres to the Gamma, we noted productivity gains upward of 50%. We had one particular set of 20mm diameter pins that required rear-end turning and grooving. On our fixed head machines, the part was taking 90 seconds and was breaking a lot of inserts when grooving. The Gamma transferred this troublesome part by producing it in 20 seconds with no vibration or tool breakages. This regular batch work fell from 1.5 days to two hours work."
This scenario was mirrored on a relief screw for a hydraulic assembly. The 13mm diameter, 90mm long screw previously took 4 minutes to machine with multiple set-ups. The screw is now machined on the Gamma 20 in one-hit in 90 seconds, taking the job from two days to a couple of hours.
On one part that required hexagonal machining with a thread at either side; Hi-Spec used to turn the part in 3.5mins and then transfer to a Haas machining centre for 4minutes of milling with engraving on multiple surfaces. This regular batch of 1500 parts would be a loss leader for Hi-Spec, as it supplied this particular customer with large quantities of work. Now, the job is profitably machined in one-hit in 90 seconds on the Tornos Gamma.
As Mr Grainger recalls: "We have a long string of jobs where the Gamma has slashed cycle times compared to our fixed head machines, but the benefits are further reaching. We have equipped the Gamma for short batch runs by rationalising on bar diameters, using 12, 16, 20 and 22mm diameter stock. We also have enough tool positions to have two roughing tools, two finishing tools as well as grooving and threading tools permanently set-up in the machine. This gives us a rapid set-up and turnaround time for jobs and dismisses the belief that sliding head machines are only for large batch runs."
In comparison to the larger fixed head machines, the Gamma 20 slashes production times by having the tool positions close to the workpiece to reduce non-cutting times. Additionally, the extremely capable back-end set-up permits simultaneous machining on front and rear spindles. Despite, the size difference between the Gamma and the larger fixed head machines, Hi-Spec has been overwhelmed by the rigidity and precision of the Gamma. On the Gamma 20 at Hi-Spec, the roughing tools are machining at 5-6mm depths of cut on free cutting steel. Furthermore, the company has produced almost 30,000 parts on the Gamma since its introduction and only used 35 turning inserts and 23 part-off inserts.
As Mr Grainger continues: "The reduced vibration through the rigidity of the machine and working close to the collet as well as the ability to run the jobs at higher speeds and feeds to suit the tooling parameters has saved us considerably on tooling costs."
"The Gamma has allowed us to accept more work from customers and it has given us significantly more capacity. The quality and surface finish of the parts has improved, as has our ability to meet tight tolerances. Another mark of quality in the Gamma is its 'warm up' period. I can turn the machine on in the morning and it is ready to run parts to tight tolerance whereas our other machines need up to an hour to warm up. The benefits are so far reaching, my only regret is not buying a Tornos sooner," concludes Mr Grainger.