Subcontractor Goes Nuts For ITC Tools
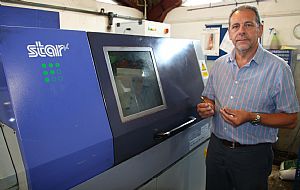
For subcontract manufacturers that operate in the globally competitive automotive industry, the high quantity production of turned parts is an arena where every possible efficiency must be found. Luckily for Basildon based SEC UK Ltd, it found its productivity saving in its favourite industry journal.
Manufacturing turbine nuts for a globally renowned diesel turbo OEM from Stainless 316L, SEC UK Ltd was witnessing poor tool life with its drills and taps. With regular batch quantities in the region of 20,000 to 30,000, tool costs were escalating as was downtime with tool changeovers. However, SEC UK Ltd Managing Director, Mr Steven Clifford found the solution when he read how drills and taps from Industrial Tooling Corporation (ITC) helped a subcontractor in a similar position to take their tool life from 250 parts to over 2000 with ITC's Widia VDS range of drills and GT and VTS taps. Mr Clifford instantly enquired and ITC's Technical Sales Manager, Mr Gary Bambrick was immediately on-hand with the solution.
Running a sliding head turning shop, SEC UK Ltd closely monitors the performance of its Star SR20 and SR32 turning centres and the cycle times of the components on each machine. Commenting upon the situation, Mr Clifford says: "We have to closely monitor every aspect of our production process as our jobs are frequently manufactured in annual quantities beyond 200,000. With such large numbers, every second counts and all aspects of the machining process have to be scrutinised and optimised."
With tool life for its existing taps running up to a maximum of 700 parts before failure, the MJ10X1.25 aerospace grade taps were costing £35 per tap. The result was a cost of £595 for each batch of 12,000 parts, which required upward of 17 taps per batch. The ITC engineer introduced the renowned Widia GT Series of TiN coated taps to the 12.5mm deep holes. The results were staggering. As Mr Clifford comments: "We trialled various taps and were a little sceptical at first. We hoped for an improvement from the ITC taps, but what followed was unbelievable. The ITC taps completed a full batch of 12,000 parts without a single breakage or changeover. They gave us an instant tool life saving of over £500 or 16 taps, not to mention the ability to eliminate 17 stoppages for tap changes. Furthermore, the ITC taps cost less than their predecessors."
Running at the same spindle speed of 500rpm on the Star SR32, the Widia taps were used in a 'peck tapping' cycle like all the taps that had been trialled before. However, the major difference was the astounding tool life. The nuts for automotive diesel turbine units are made in a variety of sizes and component families on the company's Star SR20 and SR32 sliding head turning centres and ITC has supported SEC UK Ltd throughout the process. The Tamworth cutting tool specialist has done this by supplying a range of M8 spiral fluted taps, M10X1.25 and M10X1.5 taps and also 3/8-24 UNF and UNJF spiral flute taps as well as the M14X1.5 'E' spiral flute tapping line.
Material Changes..
A couple of months ago, the performance of these taps was really put to the test, as SEC's OEM customer specified that the 316L Stainless Steel jobs would be changed to a re-drawn 316L Stainless that demonstrates a higher tensile strength and hardness level. Unfazed by the changes to the material, the Widia Tapping line from ITC threaded the holes at the same machining parameters whilst retaining their performance and tool life levels.
The success of the threading line gave SEC UK Ltd the confidence to trial ITC's milling range, despite the subcontractor being convinced that it had already investigated and installed the best performing milling line available. Already pleased with the improvements on its turbine nuts, SEC UK Ltd implemented the Widia 10mm diameter AlTiN coated four flute end mills for milling the hexagon flats on its nuts. Running at a speed of 3200rpm, the result was a 20% tool life improvement with the Widia solid carbide line completing over 6,000 parts before requiring a tool change.
"With the astounding performance of the tapping line and the impressive improvements gained through the change of milling tools, we then turned our attention to the ITC line of Widia VDS through coolant drills. Like the milling range, we were already confident that we had market leading drills on our Star machines. ITC once again proved otherwise. The family of nuts require through holes from 10 to 15mm deep and the Widia VDS drills managed to complete over 15,000 holes without a tool change, another improvement of over 20%. We soon implemented a series of solid carbide VDS 3XD drills in diameters of 4.1mm, 4.2mm, 4.9mm, 8mm and 9mm."
Looking Forward to the Future With ITC..
SEC UK Ltd has enjoyed considerable success with the ITC cutting tool range and this is set to continue as the Basildon subcontractor has now won two additional orders for similar turbine nuts that will be required in regular batches beyond 5,000off. As Mr Clifford concludes: "We are delighted to win this new business and it is credit to our investment in machine tools and our tenacity in seeking out the best available cutting tool suppliers - and ITC is undoubtedly a preferred supplier of our milling, drilling and tapping tools."