Subcontractor Irons Out Tooling Issues with ITC
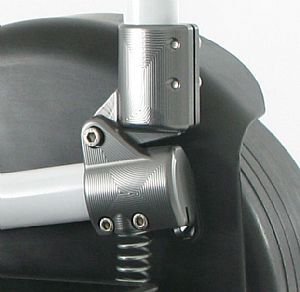
25 years after the very first Ryder Cup competition, a Lancashire based manufacturing company opened its doors for business. Like the globally renowned golf tournament, StandelDawman has also made a significant impact on the global game of golf.
Established in 1952, the company started manufacturing electric golf trolleys and related components in 1978 and can now boast remarkable production figures of over two million wheels, one million clutches and hundreds of thousands of additional golf trolley parts that include axles, gearboxes, speed controllers, handles, bag supports and frame components to name a few. Acknowledged as a market leader and the industry benchmark in the provision of electrical golf trolley components, StandelDawman has maintained its market position by investing in cutting edge technology. Adding to its machine tool acquisitions, the most recent investment has been high specification cutting tools from ITC of Tamworth.
The investment level at the Nelson based company has seen it acquire CNC twin spindle, sliding head turning centres and CNC machining centres in recent years, so acquiring the correct tooling was the next natural stage.
As a self sufficient company, the CNC machining section produces aluminium components for golf trolleys as well as tooling for its internal plastic moulding department that provides plastic mouldings for the golf trolleys. It was problems machining aluminium components in the machine shop that led to the introduction of ITC, as Engineering Director, Mr Gary Dawes recalls: “We knew our cycle times and tool life was poor and our surface finishes could be improved, so I spoke with a friend that recommended we try ITC cutters. Their technical sales engineer visited and two years later, we now have a consignment stock of their products as we were that impressed.”
Upon his first visit to the 30 employee company, ITC’s Technical Sales Engineer, Mr Jason Clark was confronted with an aluminium lighting component for a StandelDawman customer. Mr Clark introduced ITC’s 12mm diameter 2041 Cyber Series square end carbide milling cutter and changed the machining strategy to increase speeds and feeds beyond the range capabilities of the previous tooling. Targeting the rough machining process, the 2041 Series immediately reduced the cycle time from 12 minutes to 6.
As Mr Dawes continues: “The first job with an ITC cutter really opened our eyes to the capabilities and benefits of high specification tooling, especially when delivered with excellent technical support. We immediately introduced the tool to alternate jobs and consequent cycle time gains led us to acquire additional cutting tools.”
Dedicated to the rough machining of aluminium, the first 2041 Cyber Series cutter was soon accompanied by additional 6, 8, 10mm diameter cutters. Further 2041 Series tools were acquired with corner radii. The international supplier of golf trolley parts then acquired the 6 and 10mm diameter ranges of ITC’s 2052 two flute ball nosed series of ultra wear resistant micro-grain carbide cutters for finish machining and the processing of intricate forms.
The success of the aluminium series of ITC cutters led the technical representative to the steel machining department of StandelDawman. Internally producing tooling for its plastic injection moulding department, Mr Dawes introduced the high end cutters to a new trolley design that predominantly consists of plastic moulded parts. With a new trolley design requiring a new set of tooling, the Hanita 70N7 high performance solid carbide end mill series was introduced. With a considerable amount of P20 and H13 grade tool steel being machined, the 70N7 immediately made an impact. Utilised for machining mould tools for connections, mudguards and brackets, the 70N7 reduced roughing and semi finishing cycle times from over two days to a couple of hours on many of the tooling components. This drastic improvement is credit to the machining strategy and the capabilities of the 70N7 series.
Mr Dawes comments: “The Hanita high feed cutters have been a revelation to our business. The change of strategy to high feed and low depth of cut machining has reduced the stress on our machine tools whilst bringing obvious productivity benefits. These tools have been perfectly complimented by ITC’s BritCut and Hanita ball nose cutters for finish machining.”
“The surface finish on our mould tools has improved to the extent that we no longer need to polish parts after machining. We used to machine, polish, etch and anodise our mould tool parts. Taking the polishing away from the process has enabled us to save additional time and move staff from this labour intensive task. With regard to our machined trolley parts we increased the step over and altered our speeds and feeds to purposely leave a small step over mark on the parts. We deem this as a feature to signify quality and show the parts are precision machined as opposed to being cast. It is great having cutting tools of such technical excellence that we can select the quality of our surface finish.”
“ITC has catered for all our tooling needs with high performance cutters, drills and reamers. We have benefitted measurably since employing the company’s carbide tooling range with regards to productivity, tool life, surface finish and service. The company has played a considerable role in our continued success and we are delighted we chose ITC,” concludes Mr Dawes.