Subcontractor pushes five-axis to the MAXX with hyperMILL
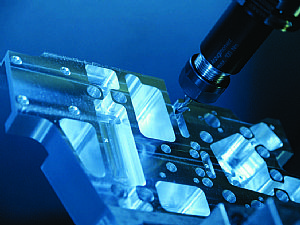
Established in 1977, Beechwood Engineering started trading in a small unit near Blackpool and its rapid expansion noted a subsequent move to a purpose built factory in Poulton-le-Fylde. The success of the company has been based on its decision to invest in advanced machine tool technology that has been complemented by the latest machine tool and CAM software systems.
As Beechwood Director, Mr Stewart Churchill recalls: “Our first investment in CNC machine tools were Bridgeport Interacts with Heidenhain controllers back in 1984. However, we noted the increased demand for complex components and the potential that a 5-axis CNC machining centre would provide. We realised that we could, not only improve our productivity with current customers but also move into new market sectors."
The turning point for Beechwood was the decision to invest in its first five-axis machine tool back in 2007, a DMG DMU 80 MonoBlock.
As Mr Churchill continued “What we didn’t want to do was invest in a new five axis machine and drive it in much the same way that we had been driving other machine tools. We looked at a wide range of suppliers and settled on the speed, power and flexibility offered by the DMG. We also realised that we needed to enhance our programming facilities to ensure that we maximised the potential of our new investment. After looking at a range of products on the market, we decided to go with the recommendations of the machine tool supplier and we installed hyperMILL supplied by OPEN MIND Technologies.”
The following three years that took the business through the recession, noted the Lancashire manufacturer buck the trend by expanding its customer base in the aerospace, formula one and medical markets. This success was credited to the new machine tool and CAM software investment that enabled Beechwood to manufacture simple or complex 5-axis parts in one-hit with astounding productivity, quality and surface finishes.
As Mr Churchill explained: "With hyperMILL, our engineers are able to take a customers' three dimensional model and apply toolpaths that not only remove material in an efficient manner but also with full control over the finishing process. Several of our older products have been migrated across from multiple set-up operations on the three-axis milling machines and been re-engineered for the five-axis machine using hyperMILL. This has delivered productivity improvements of over 20% and reduced set-ups by 15% whilst delivering cost reductions and surface finish improvements that have certainly been well received by our customers.”
“In March 2011 we had a visit from Craig Walsh the Sales Manager at OPEN MIND who reviewed our component types and recommended that we look at the latest hyperMAXX software module. At first we were sceptical towards the claimed savings and benefits as we thought our experience of removing large volumes of material using advanced pocketing cycles was unbeatable."
“However, it was immediately clear that the new hyperMAXX strategies for removing material were generating completely new toolpaths that delivered staggering results. From this, we added a second seat of hyperMILL together with the hyperMAXX module and we have standardised on this software for program generation for all our milling requirements.”
Senior Programmer, Andy Whitney commented: “With hyperMAXX we increase the speeds and feed significantly and utilise a far deeper cut than we would using traditional step-over techniques. This reduces the load on both the machine and the tooling, increasing tool life by over 50%. However, it is the time saving that hyperMAXX brings that provides the biggest benefit to us. It has enabled us to reduce machining times significantly and thus reduce our overall production costs.”
"Although we were all a little sceptical at first, within hours of installing hyperMAXX not only were we able to reduce complex programming times from hours to minutes, more importantly our machining times reduced by around 50%. This was remarkable for us, particularly as our experienced CNC engineers believed that we had previously been pushing our machine tools and the tooling as hard as we could."
“For some of our aerospace and Formula One parts with steep walls, hyperMAXX removes large volumes of material very quickly. hyperMAXX provides additional Z-level passes that takes the roughing on 3, 4 and 5-axis applications even closer to the finished size, which further reduces finish machining times."
"The latest addition to our hyperMILL system is the new five-axis Shape Offset Roughing module. This product is unique in the CADCAM market and will enable us to apply hyperMAXX toolpaths to two and three dimensional workpieces utilising the capabilities of the five axis machine tools that we now have. This is further reducing the programming burden by offering a strategy for the 5-axis machining of surfaces with a uniform offset. This is done with simple programming while avoiding the formation of ‘steps’ that would be common with Z-level roughing approaches. Improved 5-axis swarf cutting results in better surface quality whilst the new contour milling features allow for better control when using large milling tools.”
As Mr Churchill concluded “Our investments in two new Bridgeport five-axis machine tools together with the DMG machine are all controlled by hyperMILL and hyperMAXX. This will help maintain our position as a technology leader capable of delivering quality products and services to the most demanding of applications to customers throughout the UK."