Surtech Puts Success On The Table
6 September 2012
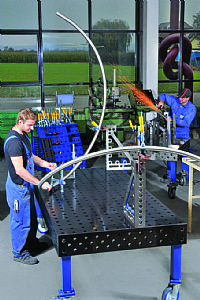
Now available from Surface Technology Products (Surtech) is the extended range of welding, jigging and fixturing tables from the globally renowned Siegmund Group. The German manufacturer that has been producing tables since 1998, has extended its product range to offer the complete work table solution. Incorporating a 3D modular positioning and clamping system for fast, precise and economical production, the tables are manufactured to a tolerance of 0.03mm.
The extended range of work stations from the Swabian company offer the end user exceptional flexibility with the scope to create a bespoke solution to meet the demands of each individual user and application. The tables are manufactured from high quality plasma nitrided steel with a hardness of over 700 Vickers to deliver scratch and erosion resistance as well as protection against impact and welding spatter adhesion.
Siegmund tables can be the answer to the problem of a shortage of skilled welders who often work with 'tack tables' that require scribing the surface and then tacking to weld stops. These stops are then ground out after the job is finished. This traditional method will eventually make the table surface like a moonscape, after which precision welding is impossible.
Applications
Some of the applications for the tables to date include robotic and manual welding stations, jigging, fixturing, measuring, monitoring and assembly stations as well as bending and folding stations. Widely used in the aerospace, automotive and general engineering sectors, some of the larger scale projects include use in the power generation, shipbuilding and construction industries.
By utilising multiple tables, the Siegmund range has been instrumental in the construction industry to produce and assemble a 53m road bridge that weighs 70 tons whilst in the shipbuilding sector the tables have formed the base for the production and assembly of yachts from 60 to 200m in length. Not only are the tables used as the assembly foundation for such large structures but also the production and assembly for over 5000m of pipeline that is used inside a luxury yacht.
Even large balustrade constructors for the building industry have utilised the work benches for fixing, flexing, grinding, welding and measuring that is involved in large construction projects. Some of the largest welding projects can be found in the construction, bridge building, ship building, nuclear energy plants, wind energy assemblies and oil drilling platforms. Simple flat or three dimensional welds are ideally suited for Siegmund’s modular welding tables where individual open frame tables can be installed to deal with virtually any size and any weight with single tables supporting up to 5,000kg and two tables joined together up to 10,000kg with a dimensions up to 2700mm x 11500mm.
In the construction sector welded assemblies for construction machinery often require more than one set up and where architects develop new designs that require flexible set up systems or three dimensional welds requiring dedicated tools, the Siegmund benches have answers for all applications.
Whilst such projects demonstrate the strength, durability and rigidity of the tables, the Basic and Professional tables are also well suited to intricate production environments such as prototype work for the automotive industry as well as clamping and robotically welding intricate and tight tolerance aerospace and medical components.
In the robotics industry, rotary turntables can be integrated with modular welding tables to robotically weld sheet metal fabrications. Such units can be configured to allow an operator to load and unload at one station whilst the robot welds on the work station. To further improve versatility, positioning systems can be added.
In the automotive industry the tables have proven a resounding success among manufacturers of racing cars, HGV's, fire engines, go carts and even golf carts. This industry benefits from the flexibility and accuracy when new dedicated welding jigs can be designed and built within hours rather than weeks. OEMs in the motorcycle industry as well as custom shops benefit from the fast jigging set-ups to test their latest prototypes.
With regard to industries that require small welding procedures, the benches have delivered remarkable results. In the case of tool boxes, enclosures and many other small items that are perfectly square, it is essential they are welded accurately and consistently to function properly. In such instances, the Siegmund modular welding tables with high precision grids and a vast range of clamping tools guarantee repeatability with accuracy.
In the sheet metal industry, set ups for welding take a lot of time and require highly skilled operators. Setting up using traditional methods take more than twice the time compared with modular welding tables with precision bores and grids. The Siegmund method not only saves time when setting up but also reduces welding time by cutting down on heat distortion. In this sector, the key benefit is that Siegmund tables are made from low carbon, high tensile steel to minimise carbon migration when stainless steel is used.
In the tube and piping industry that produces safety rails, balustrades, cylindrical assemblies for the food, dairy, pharmaceutical and beverage industry, correct alignment for accurate repeatability is a necessity. Since the majority of these tubes and pipes are made from stainless steel, it is essential that the welding table minimises carbon transfer. As the Siegmund tables are nitrided to maximise hardness, they are ideal. This is supported by a vast range of dedicated clamping tools for cylindrical parts.
With regard to subcontractors that have to deal with a wide variety of welded fabrications and are at the mercy of their customers for specifications, quality standards and most of all prices, flexibility is key. To survive, extreme flexibility and the shortest possible cycle times are essential. Only the Siegmund modular welding and jigging tables with their vast range of clamping tools can give subcontractor job shops a chance to compete.
Specifications
The heart of the table system is the ingenious universal ball bolt system. Its carefully thought out mechanical design means it can be reliably fixed in place with one hand in seconds. Comparative tests with traditional methods have shown a potential time saving of up to 40%. Modular welding tables consist of 5 sided tables with grit patterns, holes and reusable tools.
The tables are available in four standard designations, the Basic 16 and 28 or the Professional 16 or 28. Each of the four tables provides an extremely robust surface with precision holes for installing fixtures, jigs and alternate clamping devices and modules to give the end user a high precision work station regardless of the application.
The Basic 16 table is a lightweight bench with the ability to hold loads up to 500kg and is offered in four standard table dimensions that are 1.2 X0.8m, 1X1m, 1.2X1.2m or 1.5X1m. Each table is 50mm deep and incorporates a ribbed structure for additional strength. With precision 16mm diameter holes at a grid distance of 50mm over the surface of the table, which is 850mm high, the Basic 16 is the economical workbench solution for a multitude of applications. For manufacturers in need of a larger workbench, Surtech can also offer the Basic 28. With a construction of identical quality to the Basic 16, the Basic 28 has 28mm diameter holes in the surface at a grid distance of 100mm. The larger Basic 28 is capable of holding a maximum load of 1000kg and is available in 1X1m, 1.5X1m, 2X1m, 2.4X1.2m and 3X 1.5m dimensions.
For more robust manufacturing environments, Siegmund has developed its Professional Series of tables. The Professional 16 is available in table sizes from 1X0.5m through to 3X1.5m and has the ability to hold loads up to 2000kg. All tables can be extended to any size by either coupling them together or by mounting them on a common base or rails. Being manufactured from plasma nitrided steel the tables can undergo the most robust and stressful of conditions. This ensures the Professional series provides longevity far beyond tables from alternate manufacturers. When combined with the Plasma Nitrided surface coating that is only available on the Professional series, the surface and the holes for inserting clamps and fixtures are guaranteed to maintain accuracy and longevity far beyond competitor tables.
Alongside the Professional 16 is the new Professional 28 workstation. With dimensions from 1X1m up to 4X2m, the standard legs can withhold a weight of 4,000kg whilst alternate legs are available to accept a payload up to 8,000kg. The side of the table in this series is 200mm deep for side clamping and fixturing whilst the underside ribbing is spaced at 500mm for additional rigidity.
The holes in the table tops on all series have a 3mm radius to simplify the insertion of bolts and accessories. This also prevents weld spatter from sticking to the hole edges and it minimises damage at the edge of bore holes when moving heavy components.
Flexibility
The flexibility of the Siegmund tables makes the possibilities endless with multiple standard table sizes plus bespoke dimensions and hole sizes available upon request. To compliment the tables, Surtech has a complete catalogue of peripheral components and bolt-on parts to improve ease of use and capabilities. For example, the standard table legs can be replaced with height adjustable legs, legs with castors for simplified moving, high strength legs to accept larger payloads, or height adjustable legs with castors. Furthermore, the tables can be provided with no legs and only castors. This flexibility extends to bolts, magnetic bolts, clamps, stops, squares and prisms that are all available with different lengths and sizes to meet all requirements. For further details on how the Siegmund range of tables can improve your productivity and processes, please contact Surtech for further details.