Swiss Sharpening Shop Acquires Vollmer Technology
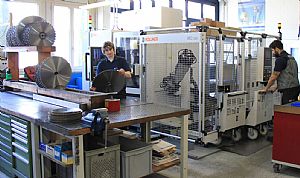
For Swiss sharpening service Siprotool AG, precision comes first when it comes to business success. For this reason, the medium sized company from Rothenburg is using Swabian sharpening technology from Vollmer. Siprotool is making use of the eight axis Vollmer CHD 270 CNC grinding machine. This machine enables the efficient and precision processing of carbide tipped circular saw blades according to the longstanding Swiss tradition.
"Our customers expect us to deliver the highest quality and precision, which is why we refuse to compromise when choosing our sharpening machinery – only the very best sharpening technology goes into use and we currently believe Vollmer is unmatched by any other supplier in the world," highlights Fredy von Flüe, Director of Siprotool AG of Rothenburg.
It is specifically the CHD 270 sharpening machine with the ND 230 robotic loading system that Fredy von Flüe decided upon. The Vollmer machine is sharpening carbide tipped circular saws for customers from both the wood and metal processing industries. Thanks to its eight CNC powered axes, carbide tipped circular saw blades can be sharpened in a chipping and free-surface setting. The Vollmer grinding unit is compact and robust, being assembled on a central block, making it possible to achieve a high level of running smoothness and therefore the highest precision during the sharpening process.
"The straightforward use and control that the CHD 270 offers makes our day-to-day use of the machine easier. Vollmer has also integrated a range of grinding programs in the software that enables universal processing of circular saws that have different geometries," explains Fredy von Flüe. "In combination with the ND 230 handling system, the CHD 270 operates on an unmanned basis around the clock, seven days a week – our current utilisation of the grinding machine now totals more than 85%."
For its automation, the sharpening machine is connected with the ND 230 handling system via the data entry system. Siprotool employees enter the planned automation sequence directly on the control panel in the context of which, only a little data on the saw blade is required on the control. The employees stack the saw blades for processing on loading trolleys beforehand. These are then guided to the sharpening machine via the handling system. When an employee swaps one of the trolleys the robot stops automatically but the grinding process is not interrupted – saving both time and energy. The ND 230 features four CNC axes – two linear axes and two tilting axes. These control the mechanical movements, and a double gripper enables rapid changeover times for the saw blades. Every loading trolley has a capacity for around 50 saws and this means the system is able to process up to 100 saw blades in a single working sequence.
"We focus on different kinds of sawing and cutting processes, we not only re-sharpen saw blades but also manufacture between around 6,000 to 7,000 bi-metal band saws per year. We also manufacture specialist tools according to customer request in accordance with the requirements for the cutting and machining industry" explains Fredy von Flüe. "We assist our customers with especially complex problems, for example we completed the precision re-sharpening and production of a circular saw for a customer in the automotive industry, in which the saw teeth are situated on the interior."
Siprotool currently employees nine staff and with a turnover of 1.8 million Swiss Francs is among the top 20 suppliers of sharpening services in Switzerland in a market with around 1,500 firms. The medium sized firm earns the lion's share of its turnover, around 70% in the re-sharpening of HSS and carbide tipped circular saws. Siprotool AG, which was established in 1987, earns the rest of its turnover with its own products, such as the Pinky diamond grinding system that is primarily used in the construction sector.
"As a sharpening service we have a broad base and with our two divisions of re-sharpening and special tools, we have two solid mainstays that we believe to have a high potential for development. We especially think that the sharpening expertise offered by Vollmer will help us. In this context, along with hard metal circular saws, we also want to align ourselves further towards diamond tools, an area where Vollmer offers an interesting range of eroding machines that correspond precisely with our precision related requirements."