TaeguTec Cuts Costs at Eaton Hydraulics
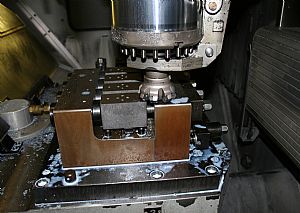
Like any globally renowned manufacturer, the Eaton Corporation is continually striving to reduce costs and create efficiency savings whilst further enhancing the component quality, that makes such a company the benchmark in its industry sector. As part of the global group, Eaton Limited in Havant, is the ‘Fluid Power Division’ that is achieving this holy grail with the support of cutting tools from TaeguTec.
As a global leader in the production of industrial hydraulic control valves for industrial, vehicle, construction, commercial and aerospace applications, Eaton produces over 400,000 NG6 valve components and a total of over four million components each year.
To achieve such staggering production targets, the South Coast based business operates over 40 CNC machining centres and a host of CNC turning centres. As with any high volume facility the cost per part, cycle time and component quality are first and foremost. To support the achieving of such targets, Eaton has an vastly experienced engineering team, that includes Mr Steve Camburn, Tony Armstrong and Gary Browning that have respectively been implementing improvements to the Turning, Drilling and Milling applications.
Eaton currently uses a number of vendors to provide the tooling for its multitude of machine tools and TaeguTec has been supplying Eaton since a chance meeting at the MACH 2004 exhibition. However, the combination of close cooperation from TaeguTec's Technical Engineer, Mr Iain Lacayo and the continual development of new products, now sees the Korean cutting tool manufacturer become a leading supplier to Eaton. What has impressed Mr Camburn is the fact that TaeguTec currently develops new tools to not only surpass the performance of its competitors but also to improve upon its own products.
With a diverse range of cast iron products ranging from high volume and a low variety mix to low volume with a high product mix, Eaton pays particular attention to production capacity. It is here that TaeguTec's attention to detail and delivering measureable results comes to the fore.
On one of the company's Cincinnati Milacron machining centres TaeguTec has introduced its new DrillRush range of indexable insert drills to improve cycle times on gray iron hydraulic valve cover components. The previous TaeguTec BHD drilling series was machining at 2200rpm with a feed rate of 220mm/min, the new 11mm diameter DrillRush with an 8XD length is now machining at a speed of 3478revs at a feed rate of 868mm/min, immediately improving cycle times by over 50% whilst improving tool life and reducing tooling costs.
The innovative new DrillRush has also been introduced to another Cincinnati machine where it was tested against a competitor drill. The 12.4mm diameter DrillRush with the new TaeguTec TT9080 insert grade operated at identical parameters to its competitor. However, the new DrillRush was able to machine 6000 holes per insert compared to 2500 with the previous drill. As a manufacturer that runs production batches, Eaton has opted to change the insert after 5000 parts to eliminate any potential tool breakages that may be caused by excessive wear. Despite being marginally more expensive than its predecessor, the new DrillRush has reduced tooling costs by 35%.
Commenting upon this performance, Mr Armstrong comments: "We are actively looking to improve cost per part and component quality across the facility. The performance of the new DrillRush on the first two machines will undoubtedly see it being introduced to other machines and processes to further enhance our profitability and productivity. Moving from the initial drilling tests, we are currently looking at our turning processes and in a relatively short period of time TaeguTec has delivered some staggering results."
Eaton is currently in the process of introducing a number of new spool products to market. The new spool designs will be manufactured in 25 different families of assembly with average production batches from 50 to 3000 parts.
For the tube shaped spools that are turned on a Traub turning centre, TaeguTec has introduced its T-Drill to improve cycle times and improve accuracy by conducting drilling and boring with one tool. The geometry and insert design of the T-Drill enables it to conduct drilling and boring operations to improve productivity for the end user. Utilising the highly rigid 3XD design to drill and then bore the through hole in the spool, the T-Drill has improved cycle times by 50% whilst reducing set-up times, eliminating additional tool changeovers and improving hole accuracy. By improving hole accuracy to allow a 0.5mm material excess for post hardening grinding, the T-Drill has consequently reduced the grinding cycle times by improving accuracy and consistency. Since the initial results with the T-Drill, the Havant based company has introduced the rigid drilling system in 18, 19, 21 and 24mm diameters.
Since TaeguTec was given its opportunity on the company’s turning centres, Mr Camburn and Mr Lacayo have worked to introduce further improvements. Adding to the success of the T-Drill and the DrillRush, TaeguTec’s multi functional T-Clamp cutting tools have been continually improving results on the company's Takisawa and Traub turning centres. The T-Clamp design enables the end users to conduct facing, grooving and parting-off with a single tool. This results in reduced tool changes and increases the capacity and capability of the tooling carousel.
The T-Clamp made an immediate impression at Eaton with a 90% tool cost saving. Working at the same machining parameters as the previous competitor insert, the T-Clamp cutter with the TT8125 insert grade machines 2500 sleeve components parts in comparison to 300 with the previous insert. This instilled confidence in the operators who were never convinced on how long the previous inserts would last. The cutting time per edge was increased from 150 to 600 minutes. The T-Clamp geometry also improved swarf removal and surface finish on the part. Staff now change the inserts every 4 to 5 days as opposed to twice daily.
This led to the T-Clamp being introduced to a Traub turning centre that regularly produces spool components. Once again working at the same parameters as its predecessor, the T-Clamp improved tool life on the 35mm diameter part with a cutting time per edge of 300 minutes as opposed to the previous 75 minutes. The tool cost saving of 82% was a typical example of extended tool life and parts produced per insert.
Also introduced to a 24mm spool part on the Traub, the T-Clamp TT9030 grade machined 600 parts per insert compared to the competitors 150 parts. This 84% tool cost saving combined with the savings on the previous parts ensured TaeguTec had further opportunities throughout the plant. Mr Camburn states: "The importance of these trails and the subsequent results go beyond cost reductions and quality improvements. The significantly extended tool life has improved operator confidence in the tooling and now permits 'lights-out' machining. This is where the real benefit lies, in the ability to machine parts around the clock without constant operator supervision."
The TaeguTec representative then trialled tooling on the company’s machining centres that are tasked with machining cast iron hydraulic valve bodies. The parts vary in complexity and hardness and often have intermittent machining that makes machining more difficult. Working closely with Eaton's Mr Gary Browning on the milling processes, TaeguTec milled a valve body with a 125mm diameter face mill with 16 inserts. With a 3mm depth of cut, Eaton was achieving 300 complete parts a day with its inserts prior to an insert change through edge wear. With a hardness level of 245HB, Eaton installed a 125mm diameter HexaMill cutter with 16 inserts to improve performance.
Running at the same parameters as its predecessor, the high feed HexaMill cutter had an insert life of 600 minutes per edge in comparison to 300 minutes per edge with the previous tool. The HexaMill doubled tool life and with 12 edges per insert, the HexaMill has three times more edges than its predecessor. The change from the 4 edge insert to the 12 edge HexaMill has reduced tooling costs by 85% and given Eaton a saving of £37 per day on the batch of 300 parts. The additional problem with the face mill cutters previously used, was that the insert seats would crack and bend and only last for up to 15 insert changes before needing to be replaced. The poor quality of the cutters delivered inconsistent performance, poor accuracy and surface finishes as well as proving costly. The HexaMill eradicated all of these issues and has delivered stable performance.
Success with the HexaMill led to the introduction of the 63mm diameter Mini HexaMill to a series of valves on another machining centre. The previous tooling supplier noted deteriorating tool life caused by small inserts on a smaller diameter cutter. The reduced insert size has a profound effect on strength and durability when high feed cutting. Initially using the TT6030 grade inserts in the 5 tooth Mini HexaMill the performance was significantly improved as the TaeguTec inserts have a double flank design as opposed to the previous single flank set-up that generated increased wear. To improve upon its own results, TaeguTec later removed the 5 insert Mini HexaMill and replaced it with a newly designed 8 insert Mini HexaMill with a new GoldRush TT6080 grade. The TT6080carbide grade with an increased number of teeth, allowed Eaton to more than double the table feed to 2.7m/min with a 3mm depth of cut. The combination of the TT6080 grade and new Mini HexaMill delivered a 90% productivity improvement and 76% cost reduction.
Improvements have gradually been made throughout the plant over the last four years and Eaton is now in a process of consolidating its tooling vendors. With the examples of TaeguTec continually introducing new innovations, the Korean manufacturer is now emerging as a primary supplier of cutting tools at Eaton.
This emergence has noted the company taking delivery of a Matrix Tool Management System that will continue to see TaeguTec cutters and inserts introduced throughout the plant. As Mr Camburn concludes: “We have gradually introduced TaeguTec to more machines as we have moved forward. The consistent performance and long tool life combined with improved swarf removal and cost benefits have been outstanding for our facility. We are confident not only in the performance of the tooling but the support that is behind the products.”