TaeguTec Supports Growth at Prestigious Manufacturer
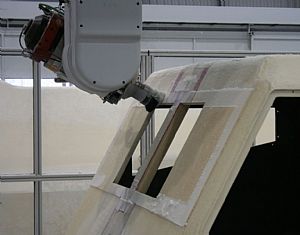
When Formaplex started business in 2001, its ambition was to become 'the best machining & tool making company in Europe'. The Havant based company has remained true to its ambition and is now one of, if not the most successful and prestigious in Europe.
Formaplex has evolved to employ over 120 staff with a turnover in excess of £25m. The bedrock for success has been the philosophy of a fast 24/7 operation and the rapid rise to success has depended on the company continuing to employ the best people and invest in the latest CNC machining technology enabling it to support industry sectors such as; motorsport, aerospace, automotive, military, marine and general industry.
Always striving to remain at the forefront of technology, Formaplex has recently acquired two high speed Famu gantry type machine centres, each with a 3m bed and also two DMG DMU 100 machines that were ordered at the recent EMO exhibition. Formaplex has also recently invested in an additional factory unit and a Poseidon gantry machining centre for machining large composite military vehicle pods.
The development of new business sectors and nurturing of customers has brought challenges with regard to machining different material types - a challenge that cutting tool supplier TaeguTec has convincingly risen to with Formaplex. Formaplex uses TaeguTec cutting tools on an exclusive basis. This confidence in the Korean cutting tool manufacturer has been earned by TaeguTec's ability to always deliver tooling solutions that will improve results for Formaplex.
As Formaplex's Operations Manager, Mr Ben Yule, comments: "We use TaeguTec cutting tools because they always strive to exceed our expectations. Our TaeguTec engineer continually introduces us to new cutting tools that improve productivity and tool life over their previous tools. One example is the new Chase2Feed series that replaced TaeguTec's BullMill. The BullMill was exceptional but the new Chase2Feed cutter is undoubtedly the best cutter I have ever used."
Formaplex utilises the indexable insert Chase2Feed series in diameters from 12 to 20mm on tool steels and additional difficult to machine materials with the HFM solid carbide range used for diameters from 6 to 12mm. With four cutting edges, the Chase2Feed machines for over four hours unmanned on hard steels at 5m/min feed rates, improving cycle times by over 30% and tool life by 20% over the previous BullMill series.
As Mr Yule continues: "We machine difficult materials during our day shift and the less demanding parts during the unmanned night shifts. However, the new Chase2Feed gives us the confidence to machine large steel mould tools unmanned overnight. This has instantly improved our production scheduling, eradicating any limitations created by the tooling. We use the through coolant Chase2Feed with TaeguTec's new TT8080 inserts. Whereas some subcontractors may machine difficult materials unmanned, our issue is the tool overhang. We use the Chase2Feed with an overhang over 100mm for processing complex 5-axis cavities and features. The rigidity and performance is beyond anything I have witnessed with surface finishes proving exceptional."
Innovative Tooling Solutions
Demonstrating its commitment to supporting Formaplex, TaeguTec provided tooling solutions for a project to produce over 200 military vehicle pods from state-of-the-art composite materials. Whilst the strength and weight properties of GFRP has been used for some time in the aerospace and wind power generation industries, this new project sees Formaplex manufacturing vehicle bodies from an extremely robust Glass Epoxy Prepeg.
Machining a vehicle pod from Glass Epoxy Prepeg took difficult machining conditions to a whole new level. With extensive experience of machining composite materials, TaeguTec worked closely with Formaplex to deliver a full tooling solution that included 5-axis milling, drilling and thread milling tools for machining the remarkably abrasive Epoxy Resin Impregnated Glass Fabric material.
Two issues that created challenges were severe tool abrasion that increases temperatures on the workpiece and tool. Additionally, the toxic gases emitted during machining and the swarf that is produced as micro fibres dictated that waste material had to be extracted with air filtration and the work envelope had to be cooled with air as opposed to circulating cutting fluids. Another issue that faced TaeguTec was the issue of delamination. To overcome this TaeguTec's Korean R&D team developed a series of new tools that required an adjustment to the tool axis angle and the geometry. The application and shaping of the PCD tooling was also a critical element to prevent material from burning during milling and slotting.
The project required tooling to meet a production schedule of two pods per day to meet the order of 200 vehicle pods and this was the reason for Formaplex's acquisition of the CMS Poseidon bridge type machining centre.
TaeguTec developed its SHD solid carbide drills with a special geometry that included a flat on the drill to act as a second diameter. This improved cycle times and prevented delamination. The new geometries enable holes to be drilled in 10 seconds with thread milling taking less than 15 seconds per hole. This speed is achieved with a drilling speed of 100m/min and a feed of 0.07mm/rev whilst giving a tool life of over 4m per drill.
For the milling process, TaeguTec introduced its 80mm diameter face mill for machining at cutting depths of 1.5mm per pass to a total depth of up to 6mm. To enhance tool life whilst machining at a speed of up to 250m/min, TaeguTec developed special PCD tipped inserts for the face mill. This philosophy was also introduced to the 20mm diameter ChaseMill that is being used to machine various pockets and cavities.
As Mr Yule concludes: "TaeguTec has delivered staggering results with its cutting tools in our metallic and pattern shops. However, the military project took our support and tooling requirements to a completely new level and as usual, TaeguTec exceeded all of our tooling demands."