Thunderbike invests in innovative solutions
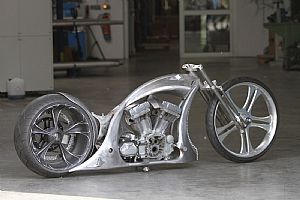
Part of what makes Thunderbike so successful, is that the leading provider of custom-tailored bikes uses a carefully selected network of manufacturing partners. Considering that individually milled parts make up 80% of the product, choosing the right partner is critical to its success.
Thunderbike relies on the hyperCAD® and hyperMILL® CAD/CAM systems from OPEN MIND and the developed NC programs are then processed on modern 5-axis machining centres equipped with TNC control units from HEIDENHAIN. The many prizes won at custom bike building competitions clearly demonstrate that the design shop that is based in the German town of Hamminkeln is doing things the right way.
The word has spread, and now half of Thunderbike’s customers are from outside of Germany. “Our custom bikes cater to a highly exclusive clientele. What makes us stand out is our attractive designs and the superior quality of our customised bikes,” says Andreas Bergerforth, Managing Director of Thunderbike.
One victory after another
The ongoing success of Thunderbike on the international stage is in part due to the bike shop’s consistent participation in renowned competitions within the bike community. Notable creations include the ‘Open Mind’ bobber or ‘Spectacular’. The Spectacular gained Thunderbike two awards in 2006 as it won the European Championship title and came in second in Sturgis. Another highlight was the ‘Build a Billy’ bike project, which involved building a high-end show bike in just three days at a trade show. The entire building process was filmed. In 2012, the ‘PainTTless’ café racer was the well-deserved winner of the World Championship in Sturgis in the U.S. So whenever Thunderbike announces a new bike project, the global biker community holds its breath – because Thunderbike is clearly setting the pace.
Unbreakable: A new bike in the making
When the ‘Unbreakable’ project bike was first announced during ‘European Bike Week’ 2013 at Austria’s Faaker Lake, which provides the backdrop of Europe’s leading Harley meeting, it was purchased right then and there. The customer’s ideas had been accounted for in the conceptual phase, which is mainly concerned with making technical drawings and scribbles. The cruiser features elaborate curves in art-deco style and has an extremely low seat. Initial drafts were made following discussions between Andreas Bergerforth and his team of engineers. As Herbert Niehues, who is in charge of custom bike production explains: "We start with the frame and the sheet metal parts. We work this way because the lead times are longest in these areas.”
The sheet metal parts are shaped manually and are then sent to a partner for a special paint job. For this bike, the entire drive technology and electronics system was designed using original Harley Davidson parts. “This means that the engine, gearbox, EFI, keyless-go, alarm system, turn signal reset and so on, is built into the bike based on proven components that can be serviced in any garage,” says Andreas Bergerforth. The newly invented girder fork is an innovative highlight. Its compact design can be raised or lowered 80mm with pneumatic cylinders. Similar to a telescopic fork, the lateral beams connect directly with the steering head and thus tightly integrate with the bike. The fork contains several milled parts. And for Thunderbike, it goes without saying that the triple clamp, indicators, wheels, radiator grille, tank cap and seat are all milled in their own machine shop. The engine and gearbox cover designs feature the characteristic parallel ribs.
Investing in the freedom to design at leisure
Ever since 2004, these aesthetic free-form surfaces have been programmed with the hyperMILL® 3D CAM/CAD system from Open Mind. As Herbert Niehues recalls: “Even back then, traditional techniques weren’t cutting it anymore when it came to implementing our sophisticated designs. The highly flexible CAD/CAM system with its cutting-edge machining strategies had me fascinated and convinced from the start.”
The software has been making optimal use of the machinery for close to ten years now. In the meantime, the bike company built up a process chain including CAD, CAM, 5-axis simultaneous machining and turn-mill technology that is unrivalled in their market segment. The machining hall is furnished with a DMC 104V Linear and a DMU 70 eVolution 5-axis milling centre with belt drive and sprocket wheel. In addition to this, the machine shop has a C42U MT 5-axis turning-milling centre from Hermle, equipped with the brand-new TNC640 HEIDENHAIN control. Incidentally, all machines, including two additional turning centres are equipped with HEIDENHAIN TNC controls. “The TNC controls are built for shop application. They superbly cater to our needs,” says Herbert Niehues.
High-performance process chain
All parts are designed and modelled using the SolidWorks CAD system. All individual parts are given a coherent design and the entire project is developed step by step in a virtual construction kit for the parts. This greatly facilitates the task of harmonising and evaluating all components in terms of their aesthetics, accuracy of fit and ease of assembly.
At the same time, complementing work is performed in hyperCAD®, in particular as regards manufacturing and supplied parts as Herbert Niehues comments: “hyperCAD® gives you an amazing amount of flexibility – in particular in the free-form area, as you approach the machining stage."
And Thunderbike certainly needs this flexibility, for example, when it comes to building the newly designed wheels for the ‘Unbreakable’ with a diameter of 26 inches for the front wheel and 21 inches for the rear one. Their inner free-form surfaces are reminiscent of turbine blades. These aesthetic highlights are first machined on the new Hermle turn-mill system equipped with a HEIDENHAIN TNC 640 from a block of aluminium at no more than 800rpm. Next, the contours are added in a 5-axis simultaneous milling job. “For us this means that we can get the job done with less re-clamping, shorter re-tooling and auxiliary processing times,” says Herbert Niehues. What used to be six job steps on three different machines has been reduced to three job steps, all of which are handled by the turning-milling centre. Given an annual workload of six to ten single-part and another 80 to 100 multi-part wheels that take up to 40 hours of machine time per wheel, this represents a considerable improvement. The hyperMILL® CAM/CAD system with its 5-axis strategies plays a crucial role in this context. Since many jobs are performed on a solid stock, the efficient stock roughing and rest material roughing strategies are applied quite frequently. What further simplifies programming is that already existing programs for component areas can be cleverly reused.
Programming is not the sole factor that determines the quality of the machined parts; the postprocessor and the graphical simulation of machining processes are just as important. After all, turn-mill jobs based on 5-axis technology require reliable collision checks in order for the operator to be sure that the planned processes are actually possible. The perfect interaction between the CAM system and the HEIDENHAIN TNC 640 is a result of the close co-operation of the two manufacturers. “The achieved surface accuracy is outstanding, and it is made possible because the new control and the machine implement the smallest details specified in the CAM system to the dot. Much like how a high resolution photograph has a stronger impact, our design is augmented by the new system,” explains Herbert Niehues.
After the initial machining step, the wheels are anodised externally. After that, they are clamped back onto the machine to mill over the outer edges, creating metallic highlights that contrast with the matte coating. The hyperMILL® CAM system and the HEIDENHAIN TNC 640 offer the perfect strategy for this processing step. Drawing on the 5-axis contour milling method, the tool connects with the surface at a fixed angle, ensuring that the width of the milling path remains constant.
Control technology made for the shop
The level of surface quality achieved as well as the real-life utility of the new turning-milling technology greatly depend on the control. “The TNC 640 control from HEIDENHAIN has taken performance to a whole new level. We love the new user interface and also receive updates on a regular basis. Key advantages include the comprehensive turning cycle package, the constant cutting speed and the cutting radius compensation,” says Herbert Niehues.