ThyssenKrupp Automates Grinding of Stainless Steel Sheets
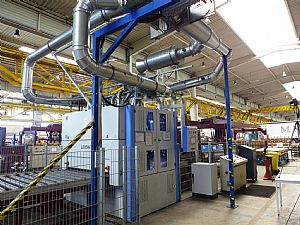
As part of the globally renowned Thyssenkrupp Group, Dortmund based ThyssenKrupp MetalServ GmbH is the world‘s largest Logistics Centre for the supply of stainless steel and alloys with over 15,000 tons of metal continuously stocked at a 130,000m2 facility with a 50,000m2 hall space.
With over 320 employees on-site, the General Manager of the Logistics Centre, Mr Marcus Raback, explains: "We make sure that around 11,500 different sheets and bars are in the programme to reach the ThyssenKrupp Schulte subsidiaries just-in-time. Besides the Metals Germany Network, the Logistics Center in Dortmund supplies customers all over Europe."
Exact Order Deliveries - Just-in-Time
Various machining operations to customer specifications are often part of a fast and economical order processing system at the Logistics Centre. These operations can be chamfering of thick plates, grinding sheets or cutting plates or tubes to size. These products find their way to manufacturers of anything elevators, escalators, industrial kitchens or the chemical and pharmaceutical industries. As Shop Floor Manager, Mr Joaquin Canhoto (Photo 2) mentions: "We offer our customers laser , plasma and waterjet cutting. We have excellent machinery in house with two flat bed lasers, three plasma cutters, three sheet metal working machines, 12 bandsaws, one robot operated circular saw plus a 3-D laser and waterjet cutter. For optimum storage we use three Kasto tower storage systems with 4000 cassettes and this allows us to handle 2500 positions daily that can be shipped overnight. Our commitment to fast and high quality deliveries is challenge to seek new ways of performing even better."
One example is the upgrading of an automatic sheet metal grinding line that was supplied by Lissmac. The goal was to make this line suitable to grind and brush mid size stainless sheets with a new belt grinding machine. The line is laid out to grind sheets in various qualities. An overhead crane places a stack of sheets on a table which is moved into the line. An automatic vacuum stacker places one sheet on an in feed roller table. Burrs from shearing are removed manually. The in-feed roller table has sheet positioning rollers to ensure that the sheets enter the grinding machine accurately . A marbling machine is placed in the same line as the sheet grinder and this can work independent from the grinder.
An automatic coating machine follows the grinder after positioning the sheets on a roller track. A second stacking unit places the coated sheets onto a movable table and the overhead crane transports the pallet with the finished sheets towards the shipping area.
Increased capacity of the sheet grinding line.
To give the 1500mm wide sheet grinding line a performance boost, ThyssenKrupp MetalServ decided to invest in a new machine that would increase the productivity. When necessary, the line runs 3 shifts per day. "Our goal was not only to have a reliable and highly productive grinder, but also to be assured of fast service when needed. That’s why we have chosen to buy a Lissmac SMD 926 profiLine grinding machine."
The integration of the Lissmac grinder into the existing line was a challenge. Together with the original supplier of the line, the Lissmac specialists and the operators, adapted all machines and handling units to the various speeds of the Lissmac grinder. Intensive programming was necessary because the Lissmac machine works with different feed speeds as well as reverse feed mode.
Finishing sheets to customers wishes
The Lissmac SMD 926 profiLine grinder has a through feed width of 1650mm, enough to process 1500mm wide sheets. With standard sheet length of around 3m, the line is layid out to also process longer sheets.
The Lissmac- dry working machine has 2 aggregates available (Photo 7), the first head is an abrasive wide belt for grinding the surface of the sheets after the burrs from the shear are removed. The abrasive belt head is followed by a round scotch brush to work either separate from the abrasive belt or in combination with the belt. The brush is placed in a cassette that makes changing the brush easy.
"The aim of this operation is to create an industrial surface finish. It is the finish we achieve from our kitchen sink or refrigerator. It is imperative that the finish across the full width and length of the sheets is absolutely spotless and constant." To achieve this, the machine must be free of vibration when grinding or brushing. A special Sorbtec frame is the basis for this. Sheets are fed through the machine by rubber covered heavy duty rollers that clamp the sheets for maximum safety. The accurately set roller drive speed is another important feature for a high quality finish. Directly beneath the belt and brush heads, hardened steel rollers are supporting the sheets during the operation. These rollers ensure a constant working pressure across the width of the sheet and are mainly responsible for a perfectly even finish.
Depending on customers wishes, the Lissmac grinder offers various finishes. The finish can be influenced by the choice of heads and the speed and working pressure parameters. Abrasive belt speed lies between 2 and 10m/s and the feed speed is from 2 up to 18m/min. The chosen grits of the belt and the brush can obtain many different finishes.
Easy to operate
Setting up the Lissmac grinder usually starts by entering the sheet thickness, which is normally between 0.7 – 3mm. The desired parameters are entered into the control unit the first time a certain job is produced. This is then saved in a programme file for follow up orders, as 1024 programmes can be stored.
In order to create exact finishes to customer wishes, ThyssenKrupp MetalServ can feed the sheets at a certain speed through the machine and also change the type of finishing heads. When making a duplo finish, the sheet is first passed under the abrasive belt head at a high speed with the brush in park-position, then returned through the machine and in the next pass brushed with a slower speed - all in full automatic mode.
Quick tool change and easy maintenance
The quality of the finish also depends on the quality and the wear pattern of the abrasive belt and the brush. Abrasive, price worthy paper backed belts are changed after 200 -300 meters of grinding. Opening the large doors for fast removal of sheet metal panels, makes it easy to clean and service the machine.
To clean and service the machine, large doors and easy removable covers are available. This way all components are within easy reach. It can be said that the Lissmac grinder contributes to the fast delivery of high quality products, in the chain of activities at the ThyssenKrupp MetalServ GMBH Logistics Centre.