Tornos Launches Next Generation Turning Centre
12 May 2015
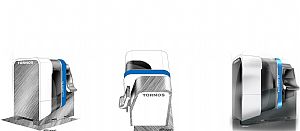
The replacement for the Tornos Deco 10 turning centre has been long anticipated, and now the Swiss manufacturer has exceeded all expectations with the new EvoDECO 10 for flexible manufacturing of bar components up to 10mm diameter. The next generation EvoDECO 10 breaks the boundaries of conventional machine tools with its four independent tooling systems, 10 numerical axes and two C-axes that are perfectly synchronised.
What this machine gives the end user is a turning centre that has been tirelessly developed to exceed the flexibility and productivity potential of any other turning centre in its class. The Tornos EvoDECO 10 achieves this with its 27 tools (up to 21 rotating) and the option to work with or without a guidebush. Something that can drastically reduce material costs by reducing bar remnant length. These features are backed by high powered motor spindles and a wide selection of peripheral devices to optimise material removal rates and production flexibility.
The EvoDECO 10 is available in two designations, the EvoDECO 10/10 or the EvoDECO 10/8. The EvoDECO 10/10 is a 10 axis machine with four independent tool systems whilst the EvoDECO 10/8 is a more cost effective solution with 8 linear axes and three independent tool systems. Both machines offer a length capacity of 100mm with a 10mm bar diameter. The main spindle generates a power output of 6.5 /10.1kW with high torque throughout the speed range that rapidly accelerates from 0 to 14,000rpm. Whilst the sub-spindle matches the speed range of the main spindle, the 5kW motor generates sufficient power for back-end working operations.
The rotating tool positions also generate considerable power output with a 1.1kW motor on all driven tool positions. This provides a speed range from 100 to 12,000rpm with 4.8Nm of constant torque. The flexibility of these modular tooling configurations is complemented by the programming interface that offers the Tornos TB-Deco system or the industry standard ISO programming language. The option of working with a standard ISO interface gives direct access to the machine's numerical control and it proves particularly practical when creating complex interfaces between the machine and external peripherals such as measurement systems. Interfacing of CAM systems is also simplified for customers using this system. The machine's 4 tool systems are synchronised via the Tornos TISIS software, which allows the four channels to be displayed and simplifies programming. Management of the machine and its peripherals is still highly intuitive thanks to the Tornos Machine Interface (TMI).
The robust build quality has been designed into the EvoDECO range from the concept stage. One of the first measures was to reinforce the chassis by upgrading the 16mm diameter ballscrews to 20mm diameter models. The rotating guide bush is also essential to the precision of the bar turning machine and this has also been redesigned with the bearings re-worked and reinforced. This new construction guarantees a more rigid assembly and upon request can also be fitted to existing Deco 10 machines equipped with a FANUC 16-iTB CNC.
Furthermore, Tornos has replaced the standard bearing in the driven tool units with a needle roller bearing. Finely hand adjusted by Tornos specialists, this development has a superior radial rigidity that makes it possible to carry out very demanding milling and drilling operations. By instilling this philosophy of rigidity throughout the EvoDECO line, Tornos has a more rigid machine that emits fewer micro-vibrations when machining. This means the tool is more stable and surface finishes are improved. With improved tool performance and reduced non-cutting times, productivity can be significantly enhanced with the new EvoDECO 10.