Tornos MultiSwiss Improves Productivity for French Automotive Subcontractor
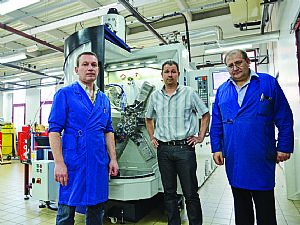
During EMO 2011, a new concept of machine forming a link between sliding headstock lathes and multi-spindle machines was unveiled by Tornos. At the time, a Tornos customer in France, Joseph Martin SA was the first company to be used as a test-bed for the MultiSwiss 6x14 turning machine.
At the end of 2012, Joseph Martin purchased a second MultiSwiss machine, this time in Chucker version. Laurent Martin, the CEO at Joseph Martin, Yves Gabillet, Technical Director and Eric Réthoré, NC Single-Spindle Workshop Manager to discover this new machine with them.
A company at the cutting edge of technology
Joseph Martin has been specialising in the production of fluid regulation components for the automotive industry for several years; offering extremely high levels of product quality to the internationally recognised automotive standard ISO TS: 16 949. This company has one of the most modern workshops, comprising 32 single-spindle and 19 multi-spindle machines as well as a collection of 50 CAM Autos. The family owned company with 180 employees and a turnover of 24milion Euros boasts a state of the art manufacturing facility that covers 7500 m2.
When Joseph Martin initially tested the MultiSwiss, it had suggested a number of ideas to Tornos about how the new product could be developed further and the Chucker was part of this feedback. As Mr Martin comments: “The second MultiSwiss machine and its design are perfect for reworking billets. All that was needed was to find a smart, economical solution to the loading problem, as we wanted to avoid having a 6-axis robot. The new machine incorporates a loading system that simply uses a vibratory feeder, so the billets are conveyed to the machining area via a pneumatic system that we have developed.”
With the new loading set-up, loading takes place in position 5 and the barrel rotates in reverse, which is an unconventional method, as Mr Yves Gabillet, the Technical Director comments: “We actually asked Tornos if it was possible to reverse the cycle to facilitate loading of the workpiece and we worked closely together to resolve this issue. The machine now turns perfectly in Chucker mode, but it can also be converted back into a machine working with bars within just a few short operations. To do this, we simply load the TB-Deco model for the ‘bar’ machine and dismantle the loading system if necessary, and the machine is ready for production using bars.
The second MultiSwiss machine is characterised by an incredible flexibility, which is made possible by the replacement of the Hirth gear with a large torque motor that turns the machine barrel. Without this technology, the feat of reversing the machine's rotation would not have been possible. In addition, the MultiSwiss torque motor is equipped with hydrostatic bearings.
Eric Réthoré, the single spindle workshop manager at Joseph Martin comments: “We were pleasantly surprised by the very long service lives of the cutting tools on the MultiSwiss with the first machine, where the high level of rigidity has a positive effect. The workpiece that we need to machine contains phosphorous and silicon, a material that is very abrasive. With a tolerance of 15 microns for the diameter and 2/100 along the length, we needed a very precise and rigid machine.”
“Following our positive experience with the first machine, a second MultiSwiss was an obvious choice for us. MultiSwiss and its hydrostatic bearings provide an unbeatable advantage in terms of the service life offered by the cutting tools. In certain cases, the gain is over 70%, which makes it a perfect choice for difficult materials. To ensure the high levels of precision and repeatability required, the machine temperature is controlled,” says Mr Rethore.
The Chucker machine is directly connected to the company's cold water network, whereas the first machine is equipped with a water chiller that makes it easy to install in any kind of environment. Filtered cutting oil is used directly in the hydrostatic bearings, and unlike systems where the hydraulic oil is mixed and changes the viscosity, the MultiSwiss oil does not required any additional maintenance.
A simple, high performance machine
The MultiSwiss has 6 powered spindles, which means the machine is programmed like 6 lathes with 3 axes. The integrated PC equipped with the TB-Deco software ensures programming is incredibly intuitive. Unlike other multi-spindle machines on the market, the MultiSwiss is very accessible, meaning a single-spindle operator can get to grips with the machine very quickly. In addition to its simple programming, the MultiSwiss certainly remains the most ergonomic machine on the market. The operator effectively ‘enters’ the machining area. This allows operators to be very close to the tool holders, thereby facilitating their changes and reducing set-up time.
As Mr Réthoré continues: “Adjustments are very quick on the machine. The Tornos tool holder system is truly practical. In the case of our Chucker set-up, we have a lubricating system integrated into the tool holders. During drilling, the bit is directly lubricated from its centre, so the system and its integration have proven highly practical during use. All adjustments are numerical, each Z-axis can be adjusted independently, and it is possible to define different offsets on each spindle. Obtaining precision workpieces on the MultiSwiss is therefore not a problem.”
Mr Yves Gabillet takes up the story, stating that: “On this type of workpiece, and with the kind of machining that we do on this machine, it is not necessary to use the preheating programme. The first workpieces are good despite the restrictive tolerances. This proves beyond doubt that the machine is well designed. At just 6 metres in length, the MultiSwiss takes up no more room in the workshop than a single-spindle machine, which gives the Tornos turning machine a serious advantage over its competitors.”