Tornos Nano Lathe Makes Big Impact for Harwin's Gecko Connectors
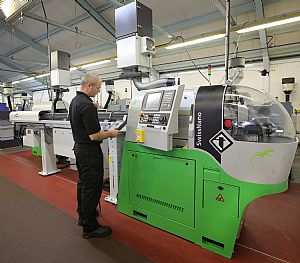
Portsmouth-based Harwin has a reputation within in the global electronics industry for the production of high reliability connectors. From its humble beginnings in 1952 as a small family-owned turning shop, Harwin has evolved into a world leading connector manufacturer that exports 80% of its products to over 90 countries.
With locations on three continents, Harwin has an active portfolio of over 50,000 connectors. To retain its position as an innovator within its customer base that includes blue chip names in the F1, aerospace, oil & gas, undersea, UAV and satellite sectors, Harwin implements a strict policy of replacing its plant and equipment on a 5-year cycle. The latest stage of this strategy was the purchase of two Tornos Nano sliding head turning centres.
In the electronic connector industry, size, weight and power output of connectors, known as the 'swap ratio', is a critical factor as the industry continually evolves. For Harwin to continually push the boundaries and produce ever-smaller connectors, the company realised that its existing machine shop needed upgrading. So, the company reviewed the machine tool market for a solution.
As Harwin's Operations Director, Paul McGuiness comments: "We are bar-feeding our sliding head lathes with 2mm copper alloy bar that is turned to produce male and female connector pins with diameters of 1mm down to 0.3mm. As industry evolves, these dimensions may get even smaller. This has been the case with our Gecko line of connectors that have a pin pitch of 1.25mm - smaller than other products that address the same application. When we looked to replace some of our machines, key issues included small factory footprint, high precision at micro sizes, cost reduction and waste elimination, speed, ease of set up and future-proofing.”
What has the Nano brought the Gecko?
Like any busy machine shop running 24/7, productivity per square meter is a key factor for Harwin. To this end, the company can achieve the same level of output in half the space of other machines. The result is that output capacity per square meter has been more than doubled.
With regard to cost, the immediate benefit was a reduction in job set-up time. The installation process and integration of the Tornos machines was further simplified by the Fanuc 0i control unit on the machines, which is similar to the control system used on its existing sliding head machines. Better yield is achieved by an improvement in process reliability.
As McGuiness says: "We are frequently working to tolerances down to +/-0.01mm, which is easily achieved on the Tornos Nano machines. Our Design department is continually making higher precision demands of the products - the Nano machines enable us to meet these demands."
Nano Makes Big Impact on the Gecko's Environment
A key to Tornos becoming a benchmark on a global stage is the ‘ever-improving, cost down, production up mantra’, and the Nano machines have instantly made an impact on material savings and power consumption. With smaller spindle motors, the two Nano machines have extremely low 6kVA power consumption, significantly less than other machines on the market. The company can potentially double its output with the same power consumption costs.
Another major saving is material consumption. As Mr McGuiness continues: "The high-performance copper alloy we use gives us great performance, but is also a significant cost. Whereas some machines left bar remnants of 300mm, the Nano turners can achieve an additional 25 parts per 3m bar length and reduce the bar remnant to just 120mm. This is a 60% saving on wastage and considerably more parts per bar. Considering we are producing tens of millions of connector pins each year, these savings are highly significant."
Process & Component Improvements.
The Gecko connector pins undergo a series of processes that involve rough and finish turning, complex form turning, drilling, slitting and swaging. All this is completed in one-hit by utilising the main and sub-spindles on the Nano machines.
"The Nano machines are undoubtedly geared for micro production. The thermal stability and rigidity of each individual facet within the Nano machine has been designed to reduce vibration. In the few short weeks since installing the Nanos, we can see they are improving our surface finishes and prolonging our tool life. This is immediately evident, but it’s too early to quantify the improvement. The linear platform of these machines also makes them remarkably quiet with no base vibration," says Mr McGuiness.
It’s the Little Things That Count…
Whilst Harwin has instantly benefited from the two Nano machines, there are a number of other technological advantages that shop floor operators at the multi-award winning Hampshire manufacturer have noticed. As Mr McGuiness confirms: "With a high precision micro-machine, bar-feeding can be an issue. However, Tornos has supplied an innovative bar-feeding unit that can feed bars below 2mm diameter with absolute ease, precision and the elimination of vibration."
"Additionally, the transfer of micro components from the work envelope to the completed component compartment is unique. With the Tornos Nano, the parts are flushed with oil prior to parting-off from the sub-spindle and then transferred neatly to a collection 'chute'. This removes all swarf and contaminants prior to ejecting the parts to a collection bin. Although our parts undergo secondary cleaning processes - and swarf removal may not be an issue for many manufacturers - when you are producing parts less than 0.5mm diameter and only a few millimetres in length it’s a major asset to remove 'all' swarf at source."
As Mr McGuiness concludes: "Our Gecko range currently has a pin pitch of 1.25mm and the industry will dictate whether this 'pitch' and the respective male and female pin dimensions eventually reduce. One thing which is certain is that Harwin now has the capacity to move to smaller component production in the future with improved design to production flexibility. For us to move from precision micro to nano production is something we would find very hard without Tornos."