Tornos Offers Complete Machining Solution With CU2007 Machining Centre
21 May 2019
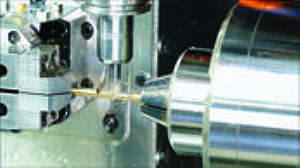
The Tornos CU 2007 milling centre and its big brother the CU 3007 offer manufacturers an all-in solution with 3 to 5-axes. The experts at Tornos can customise these machines to a high degree with the facility to equip these machining centers with an impressive multitude of options ranging from tool changers and high-pressure coolant to full automation systems that include pick-and-place robot systems.
Now, these machining centres enter the next stage of evolution with a 7-axis variant. Like all CU 2007 versions, the machine can be equipped with a 5-axis dividing head that enables even extremely complex parts to be machined. Based on the large axis travel and manifold automation systems, the idea of taking the machine to the next level has now arrived. Currently, the purchase of an expensive turn/mill centre is required to cater for a diverse range of workpieces. It is here that the CU 2007 with its 7-axes is a real alternative that offers an appealing value for money prospect.
The machine has a second dividing head that is provided both with rotary and linear axes. This enables it to be converted into a bar feeding device. With these two additional axes, the machine can easily compete with much more expensive machine tools.
Not only does the second dividing head provide the machine with a means of feeding the spindle with bar sections of appropriate length, it also enables the sixth face to be finished.
Once the front face of the workpiece is in the second dividing head, cutting can be performed and the workpiece can be removed from the bar. Once the workpiece has been clamped, the rear face can be machined using the main spindle. Upon completion, the component can be safely ejected without leaving marks. The entire system remains extremely flexible and can easily be reconfigured, depending on the requirements of the workpiece to be machined.
To round-off the autonomy of the machine, it can be equipped with a pick-and-place system. This simple yet economic and efficient automation system can be used to store bars up to a length of 330mm in a magazine located next to the machining area. It also comprises a gripper system that is attached to the spindle block. With this solution, the machine footprint has been kept to the minimum whilst optimising its ability for unmanned running.
Once the first bar has been finished, the magazine opens and the manipulator arm picks the following bar up to load it into the 5-axis dividing head. The workpiece is clamped, the magazine closes and the machining cycles can be restarted. The level of autonomy depends on the bar diameter and the length of the workpieces. Should the Pick and Place system be insufficient in terms of autonomy, the CU 2007 can be combined with a robot cell.
The six-axis robot can load and unload the workpieces and turn them over. An additional gripper system is used to handle the workpiece pallets. The integration of this robot provides the CU 2007 with a very high degree of autonomy in terms of movement. Loading, unloading, palletising, turn-over and reloading of the machining unit are carried out with unrivalled precision. This unit can even undertake intermediate storage and return the workpiece to its previous position.
The machine has 3 types of tool magazine available that have a tool capacity of 16, 24 or 40 tools. At the heart of the machine, the spindle can also be configured according to the workpiece requirements. There are three spindle types are available with a 12,000rpm high torque option, a 20,000rpm for high torque and speed and also a 40,000rpm high speed spindle option.