Tornos Provides Flexibility for Irish Subcontractor
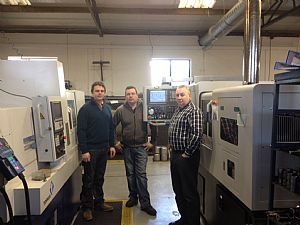
As a longstanding Tornos customer, Mann Engineering is only too familiar with the benefits that arrive from investing in technology from the Swiss machine tool builder. Having purchased a Tornos Deco sliding head turning centre over ten years ago, the Wexford subcontractor has just invested in another two machines to meet the changing needs of the marketplace.
The Irish manufacturer bought its first Tornos Deco 2000 to replace no fewer than 4 CAM Auto machines whilst reducing secondary operations. At the time, the savings from the sub spindle and driven tooling on the Deco cut some cycle times from over 2.5 minutes to less than 30 seconds. And that doesn't even touch on the floor-space, labour, lead-time and power consumption savings.
'The Times They Are a Changing'
A decade down the line and a global recession later and Mann Engineering has seen significant changes to the manufacturing landscape in Ireland. Customers are no longer ordering large batches. A New Ross business in County Wexford had to respond. As company director, Mr Rolf Fuhrmann explains: "Our regular batch sizes have fallen from 5,000 – 30,000 off to anything from 200 to 5,000, so we needed to review the feasibility of our machine tools. Nothing would match the Deco for its productivity, precision and quality levels, but for small batch runs in the region of 200, the set-up times prevented it from being a feasible option. We just couldn't compete on cost when we took set-up times into account."
Upon reviewing the marketplace and taking its existing plant list of four twin spindle triple turret Japanese turning centres into account; Mann realised it needed flexibility and productivity for parts below 38mm diameter. This is because its larger twin spindle machines would support the turning of parts up to 64mm diameter. The answer was a Tornos ST26 and a Delta 38 turning centre.
The two new additions that arrived in August and September were acquired to replace the ageing Deco machine, increase capacity and also relieve the workload on the larger twin spindle multi-axis centres. The results have been impressive.
As Mr Fuhrmann continues: "We turn our parts around for customers within a week and sometimes within 24 hours, so the critical factor in machine selection was service and support. Tornos are fully supported in Ireland by Premier Machine Tools and their excellent support over the last decade was a contributing factor in our decision process. After that, the key element was flexibility; and both machines offered this in abundance."
With a machine shop filled with a variety of Fanuc machines, the Fanuc 31i control on the new Tornos additions reduced the learning curve and created the simple transition of programs from alternate machines. As soon as the Delta 38 and ST26 were up and running, the benefits were staggering. Set-up times were instantly slashed by over 70%, which instantly made Mann Engineering competitive on smaller batch runs. As Mr Fuhrmann says: "We will do a job changeover every day and sometimes twice a day on a multiple of machines with a longer batch being loaded in the evening for lights-out machining. The new machines have instantly made us competitive whilst the productivity of the machines has been excellent."
The productivity of the new machines over the Deco and the existing twin-spindle machines has been attributed to a number of factors. Firstly, the new Tornos machines are fitted with integrated motor spindles and pneumatically activated clamping mechanism, which significantly cuts the time required for workpiece clamping and feeding bar from the Robobar SBF 326 barfeeding when compared to alternate hydraulic systems. Additionally, the kinematics of the Delta 38 and ST26 plus the modular tooling arrangements have further attributed to flexibility and cycle time savings.
As Mr Fuhrmann confirms: "Compared to hydraulic chucks and collets, the Tornos system has cut the feeding of a work piece, clamping and un-clamping times by 5 seconds per part. In addition, the tool configuration sees every tool no further than 50-60mm from the workpiece at all times whereas our turret machines will have to move the tool by up to 350mm before cutting can commence. These two factors alone have seen parts transferred from the larger machines to the Delta 38 with a cycle time reduction from 40 to 20 seconds. Another part, a stainless steel pin for specialised shelving applications was drilled, tapped and turned externally and at both ends in 60 seconds, a 15% saving from the larger machines."
These reductions are also accomplished on the ST26 where a hydraulic ram port component at Mann Engineering was cut on the larger machine in 50 seconds and then transferred to the ST26 to achieve a cycle time of less than 40 seconds. For a part that required internal and external turning, internal screw cutting and machining from both ends, the cycle time reflects the saving from the machine kinematics and tool configurations alone.
Geared for the Future...
With a healthy order book, a bulging customer base and annual growth in the region of 10%, the new Tornos machines will ensure that Mann Engineering can adapt to the marketplace, whatever it has in store. As Mr Fuhrmann concludes: "We now have a 38mm diameter machine that is relieving the workload of the larger machines, whilst the ST26 is remarkably productive, flexible and capable for all our parts below 26mm diameter. The powerful spindle, sub-spindle and rotating tool units ensure we can machine all our 304 and 316 stainless parts with outstanding material removal rates whilst the base of the machines deliver a platform for impeccable thermal stability, precision and surface finishes. We are absolutely delighted with the new machines, their performance and also the service we receive from both Tornos and Premier Machine Tools."