Tornos Supplies Turning Solution to French Automotive Manufacturer
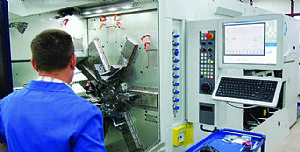
The new MultiSwiss machine that was launched at EMO had been delivered to several 'test' customers to create workpieces for several months prior to launch. The machine installed in France at Joseph Martin SA has produced more than 160,000 workpieces and proven a major success.
The company specialises in creating parts for the automotive sector that are geometrically and in terms of the accuracy difficult to machine from diameters from 0.5 to 20mm. Expectations for a new numeric multi-spindle machine with a capacity of 14mm were very high and Joseph Martin SA quickly declared their interest in testing it out. Mr Laurent Martin, CEO of Joseph Martin SA comments: "We immediately saw the major potential this machine has for creating small workpieces that we couldn't consider producing on multi-spindle cam turning machines or on single-spindle machines where productivity is not particularly high."
To make an effective comparison, the company decided to create a short workpiece, 10mm in diameter. The part required a lot of machining with a number of precise dimensions, in particular a bore with a tolerance of 8 microns. Joseph Martin SA has already created this part on its multi-spindle cam turning machines, but with results that are disappointing on the whole. Mr Martin explains: "We have produced this part on an AS14, but the tolerances required are at the limit of this machine's capabilities and the reject rate was not satisfactory."
Then, the same workpiece was created on multi-spindle turning machines with the drawback of having to extend the production time or increase the number of machines. Mr Martin told us: "Production using four different machines is not ideal, as we end up with four populations of workpieces. In terms of repeatability and reliability, there's no guarantee."
Next, the workpiece was produced on the MultiSwiss; Mr Martin states: " We were completely surprised by the results. Even without having optimised everything, the quality of the surface finishes and the machining is excellent. In addition the service life of the tools is impressive and the new hydrostatic bearings work miracles. In terms of productivity, we expect a fourfold increase compared to our multi-spindle machines, but we are going to further optimise this aspect, particularly in terms of use of the counter spindle to reach at least a fivefold increase in production."
To ensure that the MultiSwiss was really pushed to its limits, Tornos wanted 'test customers' with a perfect understanding of the single-spindle and multi-spindle 'worlds'. Joseph Martin SA has been a Tornos customer in these two domains for 65 years, and is renowned for its cutting edge skills.
"We could have chosen an operator skilled in using cam-operated multi-spindle machines or a specialist in single-spindle machining. We opted for the second option. Also, Mr Eric Réthoré, NC Single Workshop Manager knew a little about machining on multi-spindles, so it was a logical choice. We decided to place the machine at the heart of our single-spindle turning machine workshop, where a great surprise awaited the company: "We were able to simply take out an old ENC machine and its feeder and replace it with a fully-integrated MultiSwiss," Mr Martin explained. He noted how highly intuitive the MultiSwiss is and how easy it is to start up and use: " Mr Réthoré started working immediately and efficiently. The machine really has been designed with the operator in mind, and it is also so well-designed that it really makes working a pleasure".
Even though the machine has a compact footprint and everything is fully integrated, it still offers all the required peripherals such as filtration, swarf evacuation and the cooling system. Mr Martin added: "We were pleasantly surprised as the filtration system is very efficient and even after 160,000 workpieces, there was no clogging in the machine."
As this first MultiSwiss had been delivered with its chiller, Joseph Martin SA has already made provision for the peripherals to be connected to the company's power network. This can only have a positive effect on energy consumption. Another integrated element is the PC. Mr Réthoré says: "We do not do any programming on the machine, but the integrated PC has simplified how we alter programs. The fact that we also have all the machine documentation on the PC has made our life a lot easier."
To be able to fit a multi-spindle machine to a space equivalent to a single-spindle turning machine, Tornos obviously had to work a little magic and find technological solutions. The most drastic of these was the decision to have bar loading that was only 1.5 metres in length. Mr Martin told us: "This technical choice is brave, as the supply chain doesn't currently offer this option as standard. For our part, we have opted for preparation of bars internally. The solution is not ideal, but on the other hand, the loading of 'short' bars has a direct influence on the precision of the machine, simplifies handling, reduces noise and allows greater efficiency, particularly in terms of machining profiled bars. As bar changing is very quick and the scrap length is very short, feeding is not a prohibitive issue."
Regarding the hydrostatic bearings and the new torque motor indexing system Mr Martin continues:"We were already familiar with torque motor technology and we didn't have any worries about the disappearance of a Hirth gear. The machine is simpler and with the integrated measuring rules, Tornos has guaranteed precision. For us, the results are perfect. With this machine, we were also able to optimise the cutting speeds and the feed rates. Tornos has created a product of the future, the likes of which cannot be seen anywhere else in the multi-spindle machine market right now."
The reason Tornos wished to test machines in a real-life working situation over several months was so that they could take a machine to EMO that has been proven to be completely reliable. The manufacturer set up a working group so that they could be highly responsive to requests from Joseph Martin SA and the other test customers. Mr Martin said: "The conditions for the partnership were ideal. Our exchanges with Tornos were completely open and solutions could be quickly found to anything we deemed less than optimal. This significantly reduces the risk of 'teething problems'. They really listened to what we had to say and any issues were dealt with straight away."
"During the presentation of the concept, we were immediately interested, but we were asking ourselves how much it would cost. When Tornos told us their price goal, we were very surprised: this kind of solution in this price range would be a real plus," Mr Martin says.
In mid-June the first MultiSwiss installed, received an update based on the requests and remarks from Joseph Martin SA. Mr Martin concludes: "Once it has reached operating temperature, the machine's temperature response is irreproachable. The MultiSwiss has a pre-heating system, and this was another area where we put forward some ideas for Tornos to take further. We are very pleased with the machine and are already planning for the next one, the second should replace 4 single-spindle machines and we are thinking of a chucker version for the third… even though this doesn't yet exist".