Tornos Supports Growth for Precision Metrology Manufacturer
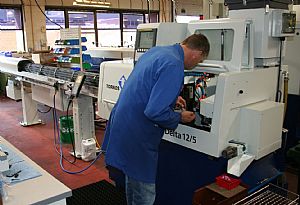
As a long standing Tornos customer, it was instinctive for Solartron Metrology (www.solartronmetrology.com) to turn to the leading supplier of sliding head turning centres when its workload and component complexity demands changed. Known as the world leader in the design and manufacture of precision dimensional and position measurement transducers and instrumentation, Solartron acquired its first Tornos machines, three Elector 16 turning centres in 1981. And with the machines standing the test of time with regards to production quality and reliability, the Swiss machine tool manufacturer has once again provided a solution by supplying a Deco 10 and Delta 12/5 in May 2011.
Since the Bognor Regis company was formed in 1973, it has grown to become a Global supplier of measurement products used in a wide variety of applications that include Precision Dimensional Measurement, Multi-channel Electronic Dimensional Gauging, Hand Tools, Positioning Systems, Process Control, Displacement Monitoring and Material Testing for a vast range of industry sectors. In 2008, the company was acquired by the Ametek Group and despite the recession, it has grown significantly over the last 5 years, increasing its staff levels to cope with the increased demand. This growth is credit to Solartron building its business to be extremely responsive to demands for a high variety of lower volume products.The company purchased further machines, a Tornos TOP200 in 1990, and two Tornos Deco 10 machines in 1999 to support its steady growth.
When Solartron commenced with its plans to buy new turning centres the company naturally reviewed the market thoroughly. As Solartron’s Technical Manager, Mr Peter Shepherd comments: “Despite being a Tornos customer; as part of a global group we had to engage in a tendering process with potential machine tool suppliers. The confidence and efficiency of the Tornos team to offer a ‘best fit’ solution to our varied component demands led to us buy a Sigma 20 in 2008. This machine replaced our three ageing Tornos Elector machines, demonstrating its capabilities to machine all our stainless steel components.
The Sigma 20 managed to replace three machines with its overlapping operations and reduced chip-to-chip times. As the company runs double shifts, five days a week, the Sigma has been running for 21 hours a day for three years. The Sigma was specified for its ability to accommodate fast changeovers, which the company demands for its vast families of parts that are produced in batches from 50 to 5000.
Proving a resounding success for the company, the influx of work led the company to add a Deco 10 and a Delta 12 to its plant list earlier this year. The two additions were bought for machining specific families of parts of varying complexity, with the Deco 10 machining the more complex parts and fitting in as a replacement for an unreliable and ageing competitor machine.
The Sigma 20 has not only improved reliability but with its high pressure through coolant of 120bar, it has slashed cycle times from 9 minutes to 1.5 minutes Meanwhile all parts machined on the Sigma are produced in less than two minutes, an exceptional saving considering all parts were previously machined in times ranging from 4 to 9 minutes. Additionally, the new Deco 10 is estimated to be at least 40% faster than its predecessor, saving Solartron 3 hours out of each 8 hour shift. A staggering seven hours a day.
The company machines bar as small as 1mm and up to 20mm diameter. For this, Tornos supplied the LNS Triton barfeed system on the Delta and Deco. This is specifically for the feeding of small bar stock and to eliminate any vibration and guarantee the bar feeding process is on par with the accuracy of the machines.” As Mr Shepherd continues: “We are machining our parts to tolerances of less than 10 microns with some dimensions having a finished tolerance of 5 micron. The parts we machine are incorporated into metrology assemblies that have many sub-micron tolerances, so accuracy and quality is paramount. To ensure we meet these parameters,
The addition of the Sigma, Delta 12 and Deco 10 has enabled Solartron to eliminate second operations that were a necessity for parts previously machined on alternate machines. This has improved component quality and statistical process control whilst reducing cycle times and inventory, with the company now drastically reducing its stock levels.
The new acquisitions at Solartron have substantially reduced subcontracting costs whilst ensuring the company retains full control over the quality of its components. Mr Shepherd concludes: "The new Tornos machines have made savings and improved our processes in ways we couldn't foresee. The remarkable productivity levels of the machines will ensure that they pay for themselves within two years. As our company continues to grow, I am confident that Tornos will support us in this growth with excellent service, support and solutions to our machining needs."