Tornos Unlocks Productivity By Retrofitting HPC System
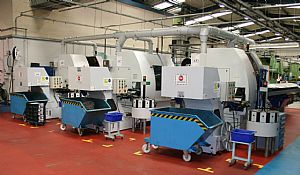
Over the last five years, Southco, a manufacturer of quick access fasteners has seen demand for its product range increase and evolve with more stainless steel products requested. For the Surrey manufacturer that has turned its parts on two Tornos Deco 20A and a Deco 26A machines for over ten years, the material change delivered poor swarf control, excessive machine downtime and the loss of full production on an unmanned nightshift – until the Tornos Engineers retrofitted a HPC system.
As a production facility that produces over a 1000 variations of its fasteners for the aerospace, automotive, medical and rail sectors, Southco witnessed swarf wrapping around tools. With swarf wrapping on each stainless job, the work envelope had to be manually cleared of swarf after each part. Dealing with this unacceptable scenario, Team leader Joe Dessent brought in the expert support of tooling suppliers such as Iscar, Sandvik and Dormer as well as cutting oil specialists Jemtech. “Five years ago stainless steel, titanium and other aluminium alloys were only 5% of our production with everything else being mild steel. This 5% has grown to 30% in five years and continues to grow, so finding a solution was a matter of urgency.”
Whilst the tooling and oil combination doubled the productivity, the company was still falling behind its production schedules as it couldn’t run unmanned on night shifts, as was previously the case. The new tooling and cutting oil eliminated the rapid ‘End of life’ of tooling and thus reduced the tooling costs and extended tool life. It was the intervention of the cutting tool engineers that suggested the three Tornos machines were retrofitted with high pressure coolant (HPC) pumps particularly for its deep hole drilling and heavy turning operations.
As Mr Dessent continues: “Following the advice from tooling engineers, we approached Tornos about retrofitting a HPC pump and nozzles to each of the four tooling platens. They immediately sent two engineers to investigate our predicament. Whilst new machines can be specified with HPC and have the coolant supplied through the back-end of the tooling, this wasn’t considered with the Tornos machines when purchased over ten years ago. So, the engineers developed a solution whereby the manifold and piping could be mounted to X1, X2, X3 and X4 positions and fed from a 120bar HPC pump that sits under the machines.”
“The Tornos engineers developed all the fixturing and manifolds, that were then manufactured locally. Solenoids were integrated, so oil flow to each of the four positions could be controlled with the machine M-Codes. Flexibility was the key, as the tool platens are constantly moving.”
At Southco, the Deco 26a is dedicated to turning four families of product that are produced in batches from 1500 to 3000 with up to 80% stock removal from the 304 and 316 stainless steel bars. Alongside the Deco 26a, the two Deco 20a machines are producing shafts in four variations that correspond with the products produced on the Deco 26a. With housings, caps and shafts being produced on the two Deco 20a machines, the swarf control issue was noted when drilling at great depths, boring, heavy rough turning, and screw cutting. The drilling required excessive pecking cycles to remove swarf whilst the boring operations created ribbon swarf that would wrap around tools and drop onto the main spindle during simultaneous operation.
The retro-fitting of the HPC systems to the three Tornos machines has enabled the 120 employee facility to increase its productivity on the Tornos sliding head turning centres, A productivity improvement of 120%. As Mr Dessent continues: “When we first started machining stainless steel and encountered the swarf issues, the problem was so disruptive that our goal was to run the machines for just one hour unmanned. We couldn’t even contemplate re-starting our ghost shift from 11pm till 6am where the machines were largely unattended – a shift we lost when we started machining stainless.”
“Now, the ghost shift has returned and we are running the Deco’s 24/5 with hourly checks on the machines. Our core products are now machined in 304 and 316 with no issues and exceptional productivity levels. Additionally, the Deco’s can support new product development projects that were previously done externally due to time pressure. The capability levels of the Deco machines afford us the confidence to try any complex part, which is increasingly the norm. We have also brought eight batch components in-house that were previously subbed out – adding another financial saving.”
“Thanks to the Tornos Engineers being able to retrofit the HPC system, we have overcome the swarf issue from machining stainless. We have improved our hourly productivity rates as well as regaining the previously lost ghost shift. Additionally, we have improved our surface finishes, tool life and our ability to produce complex parts. We now have the confidence to run any part regardless of complexity, and what’s more, we can do it unmanned. Our next step is to implement quick change tooling such as the Sandvik QS system to improve our tool changeover times whilst operating through coolant tooling systems,” concludes Mr Dessent.