Touch Probe Halves Production Costs
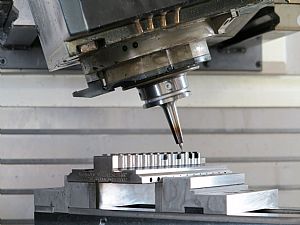
The requirements in terms of quality and accuracy in the automotive industry are continuously increasing. This also has consequences for toolmakers such as G.RAU based in Pforzheim in Germany as the basis for low tolerances in subsequent end products is created here. At G.RAU, laser measuring systems for tool measurement, workpiece touch probes and the associated FormControl software from Blum Novotest are used to produce optimum quality in its milling department. The results can be measured – both literally and figuratively.
Founded in 1877 by Gustav Rau as a manufacturing company for pressings made of gold and silver alloys, G.RAU GmbH & Co is in its sixth generation of family ownership. It now develops and produces automotive and medical instrument equipment and components from a diverse range of base metals, stainless steel, heat resistant alloys and composite materials. The portfolio of production technologies covers stamping and bending processes, extrusion and deep-drawing. With a total of 540 employees at three sites covering 34,500sq/m plus a facility in Costa Rica, toolmaking at G.RAU covers an unusually wide range of activities.
In addition to typical products such as multi-stage operation dies for stamped/bent components, deep-drawing and extrusion moulds as well as jigs and fixtures, the company creates prototypes for medical instruments.
The requirements for its machining department prior to selecting a DMG DMU 80 monoBLOCK five-axis milling centre are equally diverse. The selection criteria was based on the ability to machine up to one metre jobs while meeting extreme accuracy levels. Included in the machine's scope of delivery were a laser tool measuring system from Blum-Novotest GmbH as well as a touch probe from another manufacturer. The LaserControl Micro Compact NT tool measuring system is used for calibrating new tools and for wear measurement and compensation. The focussed laser beam makes it possible to measure the length of even extremely thin tools just as precisely as the actual diameter.
With the help of these measurements, worn and chipped spots on the cutting edges can be measured very precisely. All tools are measured from diameters of 0.5mm to 50mm. For Marcel Heinz, who heads the toolmaking production team, the advantages are obvious: "It completely eliminates the need for tool pre-setters. Instead of painstakingly measuring new tools on an external measuring station and entering the values manually into the control system, the geometry is recorded directly in the machine and stored in the tool database in the control system. This eliminates errors while reassuring us that the values recorded are actually correct. Ultimately, the tools are measured using the laser system under the same conditions they are subsequently used for machining."
The company also uses the laser system for tool breakage detection. Due to the stylus with a diameter of 4mm, the touch probe supplied with the machine proved to be useless particularly on very small workpieces. A stylus tip with a diameter of no more than 0.5mm was required for measuring inside contours. According to the supplier, this was not possible, which is why G.RAU finally turned to Blum-Novotest. Since its laser tool measuring system had already performed impressively, the new touch probe was also ordered from BLUM. Blum delivered exactly what was required, a TC52-LF compact touch probe with a 0.5mm stylus tip.
Credit to the multi-directional measuring mechanism, the BLUM probe system does not return different measurement results when probing in different directions compared with many other probes, which also helps to meet the high level of accuracy required. "A key factor that influenced the decision in favour of the TC52-LF was that BLUM could also supply measuring software with the touch probe", recalls Heinz. "Until then, we could only approach the workpiece using the touch probe and read the measurement from the screen of the machine. The FormControl software allows us to do a great deal more."
Machine operator Ralph Bauer loads the CAD model into FormControl, which runs on the same computer at G.RAU as the hyperMill CAM software. On the displayed geometry, Bauer can now define the desired measuring points, the permitted tolerances, and the measuring sequence.
The cutting knives used to trim the upper edge of a 'cup-shaped' workpiece are a good example of what the BLUM probe system is capable of in practice. Heinz outlines the challenges: "The tolerances on these components are extremely fine, just as they are on the cutting knives – whose blade clearance is just 5microns wide. The blades are arranged in a star formation and cut outwards in a radial movement. We manufacture the cutting knives from a single block of powder injected steel. One block provides two sets of twelve knives. First of all, the geometry is milled and then the cuts eroded. It all has to fit perfectly."
"These cutting tools are extremely expensive. The material is very expensive, and we then invest two days of milling time plus 50 to 60 hours of erosion." Without the touch probe, however, these tools were even more expensive, as Heinz explains further: "We simply could not manufacture these components without contour measurement and the small stylus diameter of the BLUM probe system. For this reason, these components were manufactured by a subcontractor, which cost twice as much as in-house production." Bauer mentions another key aspect: "If the production department needs a replacement part, our in-house toolmaking department can respond much more quickly than if we were to have the part made externally." explains Heinz.
The LaserControl Micro Compact NT laser measuring system also saves time, as Bauer sums up: "Instead of carrying out external measurements on presetting equipment, which then have to be manually transferred, the results are transmitted directly to the machine control system in less than one minute. This is very quick and it allows us to measure the tools during every tool change without losing too much time. This in turn also helps us achieve the high precision of our workpieces."
"The BLUM products really impressed us! With the help of the FormControl measuring software and the touch probe, we can achieve our high accuracies without difficulty. An additional machine with a pre-installed laser measuring system by Blum Novotest is already in the pipeline. We have completed all preparations to enable the use of the touch probe and FormControl on another machine."