Transition to Cost Savings is Fluid With ROCOL
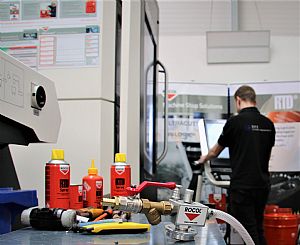
Bristol-based Nerc Precision Engineering (NPE) Ltd has been on a rapid growth trajectory since its inception in May 2018, marking the fourth anniversary of its founding with the recent installation of a DMG MORI CMX600V machining centre. Investing in prestige technology is a philosophy of the small business, and this has been highlighted with its newly formed partnership with cutting fluid specialists ITW ROCOL.
Commenting upon the growth of the business, Managing Director, Mr Konrad Nerc says: “When my wife and I started the business, we aimed to invest in the best technology to ensure that we can deliver the highest quality components and service with lead times and pricing that would be the industry benchmark. As a small and agile manufacturer with innovative technology investments that include 5-axis machining, our philosophy and customer service is enabling us to evolve rapidly.”
In the last two years, the subcontract manufacturer has invested in a DMG MORI DMU50 5-axis and a CMX600V 3-axis machining centre that is supported by zero-point clamping from Lang, cutting tools from Ceratizit, Hoffmann and Tungaloy and of course cutting fluid from ITW ROCOL. Producing everything from one-offs and prototypes to batch production, the ISO: 9001:2015 subcontract manufacturer typically services customers in the defence, offshore, automotive and general subcontract sectors with the aerospace industry rapidly emerging as its most prominent market sector.
Like any fledgling business, finding the best quality products and services is a learning curve; and this has certainly been the case for the company located near Bristol airport when considering its cutting fluids. As Konrad says: “Our initial cutting fluid supplier was a well-known name in the industry, but the quality of the fluid was quite poor. The fluid consumption was high, the coolant left a lot of residue on our components, we suffered from tramp oil and foaming, and the staff also suffered with skin irritation. We soon moved to a very high-end brand of cutting oil. This premium brand eliminated tramp oil, foaming and skin irritation for staff – the consumption was also reduced and it improved tool life and surface finishes. However, we found the poor service unacceptable, especially considering the increased cost for a barrel of oil. We eventually moved to a third vendor with a brand equally well recognised as a premium product. Whilst the quality of fluid, performance and cost were relatively similar to the second supplier – once again, it was the service and support that was lacking.”
Finding The Perfect Partner
The trial and error process led Konrad to cast a hopeful query on LinkedIn for advice and support – it was here that Ian Fenney, the Metalworking Segment Specialist from ITW ROCOL answered the call for help. “Ian came to visit us and investigate our cutting fluid requirements. Following an initial consultation, we trialled three different ROCOL fluids. Trialling more than one product was due to the diversity of the materials we were cutting, the varying operations and machining parameters and some of the products were new to market for ROCOL. ROCOL emptied and cleaned the sump of a machine, and we tried our first fluid, and the results were impressive. The quality of the fluid was excellent, and the support has been second to none.”
Since the trial commenced last year, Nerc has won a series of new customers and sizeable orders in the aerospace industry, with work in this sector now accounting for 95% of turnover. This has seen the materials machined narrow from stainless, steel, copper, brass and a multitude of ferrous and non-ferrous materials to primarily aluminium and aerospace-grade alloys. With this evolution, ITW ROCOL identified its TRI-Logic cutting fluid as the most suitable solution. The TRI-Logic range are a maximum life extreme pressure cutting fluids that demonstrate excellent inherent stability and cutting performance that improves surface finish and tool life whilst reducing foaming and odours. Furthermore, as a fluid formulated from a unique blend of specially selected additives that maximise sump life, TRI-Logic also offers excellent corrosion protection.
The Outstanding Results
To undertake the trial, ITW ROCOL supplied a 55 litre barrel of its industry-leading TRI-Logic to Nerc. This barrel was utilised in the initial trial that required the emptying and cleaning of one machine sump to demonstrate the difference between ROCOL and its fellow ‘premium brand’ rivals. With the results rapidly becoming evident the remainder of the barrel was used to continually ‘top-up’ the fluid of the remaining three machines to limit the disruption to production whilst delivering maximum results for Nerc.
From a results perspective, the fluid life has improved drastically, and oil consumption has reduced by over 50%. Logic would tell any engineer that a 50% consumption reduction would naturally reduce the fluid costs by 50%, yielding a huge saving. However, the ITW ROCOL TRI-Logic EP has a retail cost 50% less than its rival premium brands. With a 50% reduction in the purchase price and a 50% fluid consumption reduction, the savings are staggering.
As Konrad beams with delight: “The 50% cost reduction is something that every small business wants to take advantage of, but when the consumption also reduces by 50%, the cost of coolant stops being a concern. The initial 55-litre barrel lasted from July to February and we have recently taken delivery of a 200-litre drum of TRI-Logic. Our initial projections were that ROCOL’s TRI-Logic would provide a cutting fluid consumption reduction of 25%. However, with the new aerospace work, we are running four machining centres up to 16 hours a day and we are busier than ever before. Running at optimal production rates, we are recognising that our cutting fluid consumption is at least 50% less.”
The performance of the two previous premium brands far exceeded that of the first brand used by Nerc in terms of extended tool life, sump life, improved surface finishes, a reduction in foaming, tramp oil, oil residue on parts and skin irritation. The ITW ROCOL TRI-Logic has matched and even exceeded the performance of its rival brands in all areas.
The 200-litre barrel of ITW ROCOL’s TRI-Logic high-performance cutting fluid has been supplied with an automatic fluid mixer that accurately mixes and dispenses the correct dilution of cutting fluid and water. With a built-in double check valve and vacuum breaker that is WRAS (Water Regulations Advisory Scheme) approved, the system meets the most stringent of safety requirements for category 3 fluids and ISO EN: 1717 regulations. Fast, efficient and easy to use, the mixing station always ensures that Nerc Precision has the optimal fluid concentration in its machine tools.
“For our business, specifying cutting fluid has been the hardest thing to get right and find an improvement. Unlike capital and ancillary equipment, the challenges with cutting fluid can be the most difficult aspect of the business to get right. The challenge of trialling new coolants has several implications. For example, emptying and cleaning machines to trial fluids can be time-consuming with machine downtime – and then there is the concern that the new fluid may not improve your productivity, fluid life and tool life; or it may not be compatible with the materials machined. There is also concern over tramp oil, foaming, residue on components, skin irritation, disposal and much more. Thankfully, ROCOL resolved all of this, and the results have been fantastic. ROCOL has an extremely honest approach – they said their fluids would work and they do. ROCOL doesn’t just ‘talk the talk’, their cutting fluids also ‘walk the walk’. The previous premium brands we tried improved performance, tool life and surface finishes over the first fluid we tried – ROCOL has exceeded the performance of these fluids whilst reducing our consumption and costs,” says Konrad.
Setting the Standards With Service
With service and support from all three of its previous cutting fluid vendors being an issue for Nerc Precision, Konrad concludes: “The service and support from ROCOL is second to none. They reviewed our business, listened to our concerns and then provided a solution that has exceeded everything else that went before. Most importantly, a ROCOL engineer is always on call to check our machines and support us accordingly the support us in checking the fluid levels in the machines, the ph levels and fluid concentration. We couldn’t ask for a better support.”