Two giants creating the future of wind energy
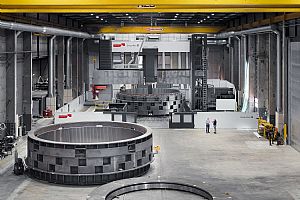
HACO A/S, a Danish family-owned company, is now equipped for the future of wind energy by installing its second large machine from Starrag. The company can now machine massive rotor housings and brake discs for offshore wind turbines in the 14 to 15 megawatt class more efficiently and precisely than ever before.
The small town of Rødekro in southern Denmark, near the German-Danish border, is developing into a logistical hub for the offshore wind industry. Its proximity to the port of Esbjerg, Northern Europe's leading offshore wind hub, and the ports of Aabenraa and Sønderborg enables efficient transport routes for wind energy components. The close cooperation between HACO and SM Industrie A/S, a leading supplier of steel wind energy components, exemplifies sustainable logistics. The new machine duo will be used in a hall on SM Industrie's premises.
Machine duo with standardised operation
A large Droop+Rein gantry machine with a travelling gantry, capable of flexibly machining very large workpieces in a single clamping operation, has been installed and running since the beginning of 2024. Recently, it has been complemented by another very large Dörries gantry machine with a fixed gantry and sliding base. Despite their differences, both machines share the same core components, simplifying maintenance and operation.
The new large gantry machine significantly expands HACO's machining range. Thanks to its enhanced main drive and increased swing diameter of the workpiece, it is now possible to manufacture larger welded rotor housings and other substantial components with precision. "Our two large machines – two true giants – are now in production," says a delighted Hubert Erz, Senior Consultant Sales/Renewables at Starrag. "We are setting a new benchmark in machining workpieces for gearless wind turbines in the 14 and 15 megawatt power classes. The focus here is primarily on rotor housings, generator housings and brake discs, both of which currently have a diameter of around 9m and are manufactured with an accuracy range of +/- 0.1mm.
When the specifications call for high precision …
The wind energy industry typically demands tight tolerances in its specifications for large components such as rotor housings and brake discs. "Regardless of the size of the machine, it is important to precisely calculate and dimension the main components using modern design tools. We achieve the first static compensation as early as the moulding stage,” explains Erz. In addition, there are precisely adjustable mechanical components and final electronic fine-tuning, as well as a precisely designed machine foundation that considers static and dynamic loads.
HACO also prioritises production reliability and continuity. That's why the family-run company deliberately decided against the latest Siemens control system. Instead, Managing Director Henning Albrechtsen favours the tried-and-tested version: "We rely on tried-and-tested technologies. This not only ensures production reliability, but also the flexibility of our employees."
Better safe than sorry
Instead, the managing director invested in programming and simulation. New post-processors with an integrated simulation module from the Starrag UK subsidiary TTL enabled the team to create NC programmes in the main factory and simulate the machining process. This included measuring programmes in advance, which significantly increases productive machine running time. In addition, the second machine was equipped with a modern magazine concept with automatic loading and unloading of tools plus six machining heads for turning, milling and drilling. This provides flexible and precise machining of large parts in a single clamping operation.
The two 870-ton machines required a foundation capable of withstanding the enormous static and dynamic loads necessary for precise machining. During the design phase, Starrag implemented extensive assembly and handling precautions to ensure that these substantial components could be transported and aligned accurately. A central feature is the two-storey basement, which provides a stable base and facilitates access to central components. HACO and Starrag also addressed this challenge collaboratively. The customer is satisfied: "We integrated units into the foundation, so that noise emissions were virtually eliminated – a clear plus point for the quality of work."
Sustainable concepts for the wind energy industry
Starrag's LPMS (Large Parts Machining Systems) business unit created the new machine duo. This unit specialises in innovative manufacturing solutions for large parts and is guided by the strict criteria of the VDMA BLUECOMPETENCE label. This also had a lasting effect on this project.
Modern, energy-optimised components, advanced drive technology, and the recovery of surplus energy ensure reduced energy consumption at HACO's plant in Rødekro. These measures lower material consumption, reduce waste, and optimise energy use – a competitive advantage for industries that focus on sustainability.
Machine duo sets the benchmark
The investment in two large machines offers excellent opportunities for machining current and future large components in the wind energy sector. The intentionally chosen flexible design and equipment of both machines impose virtually no limits on machining large components. Erz says: "The courage of Henning Albrechtsen and his team is now paying off. Together, we have created a new plant that will enable our regular Danish customers to manufacture future, larger generations of wind turbines and XXL components sustainably, efficiently and reliably."
Henning Albrechtsen, Managing Director of HACO, meets the high demands of the wind energy industry with three innovative strategies. Alluding to this, Henning says: “For years, we have been practising complete machining with our Dörries machines at our main site in Barrit, using as few clamping operations as possible, including turning, drilling and milling. The experience flowed directly into the planning of our systems in Rødekro. The larger the workpieces, the more complex the handling becomes. Reason enough for us to develop a clamping device with which rotor housings, for example, can be finished in a single clamping operation.”
“Our machined components, from rotor housings, brake discs and stator laminations, remain predominantly welded workpieces that will be manufactured in larger dimensions in the future. At the same time, our product portfolio has expanded. In addition to traditional parts, we now also machine castings, such as generator housings and adapter components for connecting the nacelle and tower. This puts us in an ideal position to meet the requirements of the next generation of wind turbines.”