Unicut Dispatches Competition With Continued Investment
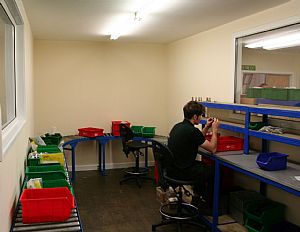
With over 1.5milion parts being produced on a monthly basis, Unicut Precision has to run an extremely efficient operation to ensure this vast quantity of components are all manufactured, inspected, packaged and dispatched to the Kanban or JIT demands of its multitude of customers. To ensure the smooth through-flow of work at Unicut, the company has invested £27,000 in a dedicated inspection, packaging, storage and dispatch department that was completed in October.
The new department has been established to increase the storage and flexibility needs of a business that has grown by over 25% in the last 12 months, with turnover doubling in just two years. The deburring, sorting, counting and packaging was previously in one department with shop floor staff all contributing to the extensive effort to get parts out of the door each month. To improve workflow, efficiency and quality, the Welwyn Garden City company has built the dedicated department with three separate rooms within the new structure.
The new layout incorporates an area for visual final inspection of parts whereby the components placed in coloured trays are moved along a roller conveyor system for inspection. Once inspected, the trays are moved to the next area for picking and packing. This room ensures that all customers parts are counted, boxed and labelled to the exact demands of the end user. With an abundance of Long Term Agreements with prestigious OEM's, many of the parts produced by Unicut are tight tolerance parts with impeccible surface finishes. These parts often demand particular care and attention when packaging to avoid scratching or any other potential form of damage.
Once the parts are allocated to their customer specific boxes or packaging, they are labelled and moved to the new goods-out area. The goods-out area incorporates a new storage facility whereby parts can be booked into stock ready for shipping or shipped out immediately, depending upon the customer delivery requirements.
All of this is overseen by a PSL Datatrack system that has been continually upgraded with new modules since its initial introduction in 2004. The company has progressed from working on a spreadsheet basis to now moving paperless with its efficient on-line system. The PSL Datatrack system at Unicut Precision has for some time offered everything from quote and order raising, capacity scheduling and material sourcing and traceability through to shop-floor data collection regarding the parts produced and cycle times through to dispatch. However, with the new dispatch department at Unicut, the company now has a visual traffic light system from PSL Datatrack that operates throughout the company with large screen displays to give shop-floor staff an update on each job.
As Unicut Precision's Managing Director, Mr Jason Nicholson comments: "The new traffic light system from PSL Datatrack is visually available for all staff, with screens throughout our facility to enable the shop floor to be fully aware of the progress of each job. These status boards enable staff to extract information from the system rather than be informed by the office of the progress of each job and what job takes priority. The status boards inform the staff in the new dispatch department what to prepare and package for delivery rather than waiting for jobs to come in.. This new traffic light system combined with the building of the new department has improved what was already an efficient process."
Highlighting the efficiency of the new department and the visual status boards from PSL Datatrack, Unicut Precision has now taken its on-time delivery levels from an impressive 93% to over 98%. Considering the new dispatch department and traffic light system has only been in place for a matter of weeks, the on-time delivery at Unicut will hit 100%. Such efficient processing from order raising through to component delivery, is yet another reason why Unicut is filling its extending customer base with confidence in its quality, service and delivery. Once again proving that Unicut Precision offers the 'Perfect Manufacturing Environment'.