Unicut Enhances Lean Credentials with new Durr Cleaning Plant
11 September 2013
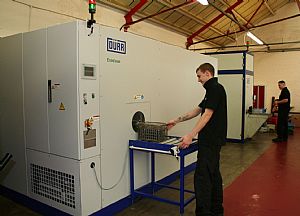
The ongoing commitment to investment at Unicut Precision has now seen the Welwyn Garden City subcontract manufacturer install the UK's first Durr EcoCBase W3 component cleaning system. Always at the forefront of technology, the purchase of the UK's first EcoCBase W3 machine not only enables Unicut to clean all its components in-house, it gives the company component cleaning capabilities and quality far beyond its competitors.
The arrival of the Durr EcoCBase system at the end of 2012 coincides with the completion of the company's new dispatch department. The Durr EcoCBase 3 tank aqueous system incorporates a washing, rinsing and passivation station that enables Unicut to maintain in-house control of processes that were previously subcontracted out. The Durr arrival is part of a wider strategy to create an efficient through-flow for the 1.5million components the company produces each month.
With an increasing number of new machine tools to cater for the expanding diversity of the industry sectors and component types being produced, Unicut has machine tools running both soluble coolants and neat oils. This placed increased capacity demands on the existing Durr Mineo 85C hydrocarbon solvent cleaning system and also noted increased levels of parts being cleaned externally. As Unicut's production capacity grew, the diversity of contamination including mineral oils and coolants also increased. This meant that a truly flexible approach to a range of cleaning requirements was needed. The Dürr W3 and Minio machines provide this flexibility and control. The Durr acquisition is an investment in process control and stability for Unicut. It will further reduce lead times and enhance the company's 'lean' credentials.
The arrival of the new cleaning plant now enables Unicut to wash, remove excess swarf and dry its stainless steel parts and alternate material types in-house. This is credit to the cleaning system that has three completely separate tanks for washing, rinsing, mineral removal and drying. Commenting upon the investment, Unicut Precision Sales Director, Mr Stuart Lawson says: "We are now producing upwards of 1.5 million parts each month. To retain complete control over our through-flow of work we have to run a very slick operation. By bringing the cleaning of all our parts in-house, we have greater process and quality control, improved flexibility and improved lead-times. Unlike investing in a machine tool to generate increased capacity or profitability, the Durr EcoCBase is an investment in our business and a statement to our customers that we are continually looking at every aspect of our business to enhance the customer experience. By installing the £150,000 EcoCBase we have made a statement of our commitment to excellence and it is this commitment to customer service that retains our position as the UK's benchmark subcontract manufacturer of turned parts."
Highlighting the capabilities of the Durr EcoCBase W3 system and the benefits to Unicut, Durr EcoClean's Sales Director, Mr Matt Copper comments: "During initial consultation with Unicut, it was apparent that the company wanted a system that could provide fast turnaround cleaning with complete flexibility for the cleaning of a diverse range of parts. The focus for Unicut was lead time reduction and complete process control - the EcoCBase W3 has delivered this."
The new EcoCBase W3 has eight pre-set programs that epitomise flexibility. For example, Unicut can program the machine by material type or cleaning temperature. Short cleaning and rinsing cycles or alternately more extensive cleaning cycles can be set on the EcoCBase. The flexibility of the Durr enables parts to undergo a short 2, 3, 4 minute wash or a more comprehensive 10 minute cycle, individually utilising each tank as required.
The new W3 cleaning system incorporates new innovations such as an infra-red, vacuum and vacuum drying process that can be used individually or simultaneously. For Unicut, this improves cycle times whilst ensuring that blind holds and intricate features have all excess swarf removed. Additionally, the Durr EcoCBase W3 is the company's first system that has individual piping, filtration and pumps for each of the three tanks. This delivers almost complete separation of the media between the three tanks to enhance the cleaning processes as well as improving the service and maintenance requirements of the EcoCBase W3.