Unicut Precision Wins Prestigious Eaton Hydraulics Contract
28 June 2014
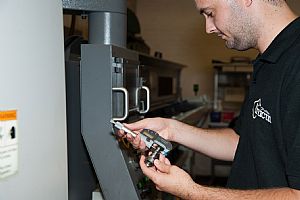
After four years as a subcontract machining supplier to the globally acclaimed hydraulic power division of the Eaton Corporation, Unicut Precision has won a 4 year contract worth over £3m to supply cartridge bodies.
In 2013, the Havant Division of the Eaton Corporation set about streamlining its supplier base by asking its specialist hydraulic subcontract suppliers to re-tender for the next long-term manufacturing contract. The aim of Eaton was to streamline and rationalise its purchasing and supply strategy by reducing its subcontractor base to leave a reduced number of suppliers capable of reducing costs whilst maintaining exceptional quality and delivery levels.
To succeed over its competitors, Unicut Precision proposed a plan for a 'focus factory dedicated to the Eaton contract. The bones of the proposal from Welwyn Garden City based Unicut, included a two-year investment plan to enhance logistics, quality and supply flexibility that will surpass anything available from alternate subcontractors whilst continually and sustainably reducing costs.
To implement this, Unicut provided the option of 24/7 production and improved lead-times. So far, this has involved an investment in an extended 4,400sq/ft dedicated Eaton 'focus factory' with two new Index C200 multi-axis turning centres costing up to £1m to improve productivity levels. Alongside the new machines, two existing Miyano and Citizen machines have been transferred to the facility. To further optimise lead-times, Unicut has also invested £74,000 in quick change tooling and pre-setting systems to reduce programming and set-up times.
As Unicut Precision's Managing Director, Mr Jason Nicholson comments: "The whole philosophy of our proposal was to introduce new technology and production techniques to enhance process control, supply lines and quality through every element of the process. Simultaneously, we had to demonstrate we could sustainably deliver cost-down results for the customer whilst maintaining a profit margin. We have committed to an annual cost down in the region of 3% per annum and to sustain this, we highlighted savings in every element of the process."
The Cost Down Strategy
The investment in the facility, two new machining cells and quick change tooling was just the first step in Unicut's long term strategy. With meticulous planning, Unicut calculated that with the increased 'focus factory' space and an increased annual consumption of steel from 50 tonnes to 250 for Eaton; steel stock/storage and its order quantities could be increased by ordering direct from the mill. This instantly eliminated third party margins and delivered a cost-down for Eaton.
Another process identified to reduce costs is the plating of the steel components. The steel cartridge bodies that are essentially safety valves for the hydraulics industry require either zinc or nickel plating. Currently a subcontracted service, Unicut identified that by acquiring its own in-house plating plant, it could improve process control, quality, lead times and essentially reduce costs even further. To eliminate inconsistent plating quality and delivery schedules, Unicut committed to investing over £48,000 in year two of the project to reduce its plating costs by an impressive 18%.
Commenting upon the steel stocking strategy and the introduction of an internal plating line, Mr Nicholson continues: "Our contract with Eaton to supply over 380,000 components each year is based on a Just-In-Time critical supply line agreement. So, regardless of how productive our machine tools are, we have to nail down every element of the process to the most finite detail to guarantee JIT delivery of components to the highest quality levels. We already produce over 16 million parts per annum for our existing customer base, primarily on JIT or Kanban contracts to 100% delivery success, but we cannot rest on this exceptional record. We are always striving to improve our quality and process stability."
To produce over 16 million parts each year, accurate scheduling and delivery planning is critical. To cater for this mammoth production and logistical task, Unicut has recently invested in a state-of-the-art traffic light system from PSL DataTrack to support its dedicated dispatch department. The highly visible dispatch status boards enables all production staff to conduct 'live' monitoring and progress of each and every order that flows through the company. Existing Eaton consignment stock is managed and stored on this system and with an already exceptional delivery record, it undoubtedly filled Eaton with confidence in Unicut's ability to deliver on the contract for over 66 new product variations.
Whilst delivering to deadline is critical; delivering to Eaton's extremely high quality levels is another matter. Despite investing the most precise machine tools available, Unicut's next investment earmarked within the proposal is the planned installation of an additional CMM dedicated to the Eaton 'focus factory' project. The integrated CMM will comply with Unicut's existing SPC procedures to provide automatically recorded and stored data. For Eaton, the benefit will be complete traceability records and data reports for every production run that is delivered.
Concluding on this prestigious contract, Mr Nicholson states: "By winning this contract and committing to technology investments that will deliver annual cost down for the customer, we have demonstrated our desire to be the benchmark in precision subcontract production. However, regardless of our technology, production systems and process controls and stability - the key to our continued growth and success is our dedicated and highly skilled staff. Winning prestigious long term contracts is the holy grail for subcontract manufacturers and for us to attain this, our team were fully involved in each and every step of the process. Without the support of the whole team, it wouldn't have been possible to conduct the meticulous planning and detail analysis that was necessary to win the business."