Unilathe on the Rail-Road To Success With TaeguTec
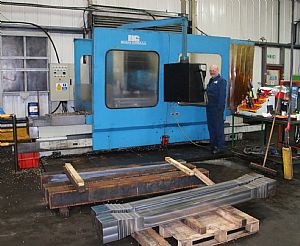
The prolonged depression in the oil & gas sector is impacting business for subcontractors the length and breadth of the UK. However, Unilathe is a subcontract manufacturer that sees the downturn as a small 'bump in the road' credit to its diversification strategy and more importantly its £3 million machine tool investment over the last four years.
The investment in two heavy duty mill/turn centres from Mazak and WFL have been complimented by vertical turning centres from Honor Seiki and Doosan. This has improved flexibility, productivity and reduced set-ups to improve overall through-flow. For Unilathe, this investment has enabled the company to ride the cost-down demands of the oil & gas supply chain whilst improving the productivity and lead-times on its large components for the aerospace, hydraulics, rail and general engineering sectors.
The 100+ employee business has increased capacity by over 20% with its machine investment, whilst productivity has also soared. However, like any established subcontractor, Unilathe realises that machine tools are only one factor in the overall picture of a business. To this end, the AS: 9100 accredited company has employed the expertise of TaeguTec to maximise the productivity of its machine tools.
As Unilathe's Manufacturing Director, Mr Mark Oakley comments: "Our work is extremely diverse with regard to material type, part size and machining process, so we use a wide variety of cutting tools from TaeguTec to support our needs. We've worked with TaeguTec for over 15 years and this longstanding relationship is based on excellent support and continuous product innovation that sees a TaeguTec engineer frequently visit with new products to continually improve our productivity and processes."
A glowing reference to this endorsement was the market introduction of TaeguTec's Chase2Hepta face milling cutter in 2013. TaeguTec's Technical Sales Engineer, Mr John Handley introduced the Chase2Hepta to a troublesome job and the consequent success now sees the Chase2Hepta designated as the face mill of choice for Unilathe's heavy stock removal demands.
Quantifying the Benefits..
Like many subcontractors producing 1-off's and small batches, quantifying benefits can often be difficult. However, Unilathe won a contract to produce 150 large carbon steel forged 'mud valves' for the oil & gas sector that instantly started to wear and break inserts on an alternate face-mill. The unacceptable performance of this competitor cutter gave the Chase2Hepta an opportunity to shine.
Running on a Toyoda horizontal machining centre with a BT50 spindle, the 100mm diameter Chase2Hepta with seven insert pockets and double sided inserts offered a 15% reduction in cost-per-insert compared to its predecessor. But we all know its about performance and not cost!
To this end, the new Chase2Hepta increased cutting speed from 190 to 220m/min and the spindle speed from 620 to 700rpm. To coincide with these parameters, TaeguTec increased the feed rate from 800mm/min to 1500mm/min whilst retaining the same 3mm depth of cut as the previous tool. The result was a cutting time reduction of 45% from 26 to 14 minutes for each of the four flange faces on the mud valve. This recorded a metal removal rate of 309cm3/min compared to the previous 167cm3/min. Overall, the insert cost saving of £270 and the productivity improvement that impacts the chargeable rate of the machine tool, delivered a total financial saving of £1800 or 43% for this one batch of parts.
Whilst the financial benefit, tool life and productivity improvement were instantly realised the Chase2Hepta delivered even more. The XNMU right hand helical cutting edge insert with a sharp positive chip-former in the TT9080 grade also improved surface finish, chip flow and reduced the vibration and forces on the machine spindle. In fact, the spindle monitoring on the Toyoda machine recorded the power consumption of the smooth cutting TaeguTec Chase2Hepta was 38% during heavy cutting whilst the previous tool was drawing over 85% spindle power due to its inferior insert geometry and cutting action.
The Bigger Picture..
Following the successful implementation of the Chase2Hepta that was proven on the mud valves in 2013, the TaeguTec face mill is now the rough machining cutter of choice for the £7.5m turnover business. As Mr Mark Oakley continues: "In the last couple of years we have successfully applied the Chase2Hepta to parts for the rail, aerospace, oil & gas and heavy industry sectors. This has included components produced from duplex, stainless steel, mild steel and various cast materials. For each of the material types and machining parameters TaeguTec has supplied the inserts for the job. For example, we now apply the ML geometry insert with TaeguTec's TT8080 grade to duplex and stainless parts and the M geometry TT9080 grade to mild steel parts."
"Regardless of geometry or grade, in every instance the Chase2Hepta has reduced cycle times, tooling costs, spindle stress and vibration whilst simultaneously improving component quality, consistency and surface finishes. The Chase2Hepta is undoubtedly the preferred face mill for our 45 degree milling needs. The success of this tool has been replicated with other tools on alternate machines and TaeguTec are making a significant contribution to our productivity and tooling cost reductions."
The remarkable success of the Chase2Hepta at Unilathe has been paralleled with the implementation of other TaeguTec tools such as the ChaseMold and ChaseBall. The combined success of these tools has contributed to Unilathe reducing its average monthly tooling consumption from £35,000 to £25,000.
The Next Step..
As with any subcontract company, Unilathe will continually aim to reduce tooling costs and consumption through implementing new tooling innovations that simultaneously improve the productivity of its machine tool investments. To support Unilathe on this journey, TaeguTec is now looking to trial the new ChaseHepta milling cutter that has just been launched.
As TaeguTec's John Handley comments: "The Chase2Hepta was developed for robust, heavy duty machine tools with high stock removal rates and the economic benefits of double sided inserts. Whilst this has been remarkably successful on BT50 machines, the new ChaseHepta is a brand new innovation that aims to bring these benefits to lower powered, less robust platforms. This makes the new tool suitable for BT40 spindle configurations and also reducing cutting forces on unstable, thin walled components. This will be delivered through a new cutter body design and a single seven sided positive insert geometry, which will undoubtedly help Unilathe to continue reducing its tooling costs as we move into 2016."