Upgrading to hyperMILL
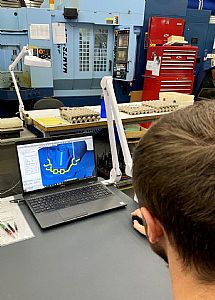
When Shearline Precision Engineering Ltd recently added to its advanced 5-axis machine tool inventory, the Ely based company recognised that it needed to upgrade its CAM software to maximise the capabilities of its investment. That is why the company has invested in the hyperMILL CAM software from OPEN MIND Technologies.
As part of the Shearline Group that operates out of an 8500sq/m manufacturing space in Cambridgeshire, Shearline Precision Engineering Ltd adheres to standards such as AS:9100, ISO:9001 and ISO: 14001; manufacturing everything from simple to extremely complex components for customers in the aerospace, instrumentation, motorsport, medical, packaging, power generation and printing industries. It is the complex production tasks on its 5-axis investments that have led the manufacturer to OPEN MIND Technologies.
As Simon Cooper from Shearline Precision Engineering Ltd says: “One of the key reasons that triggered us into getting the hyperMILL software from OPEN MIND Technologies is that we were already using a relatively successful CAD/CAM package, but when it came to the top end, jobs that required 3D scanning and simultaneous machining on our latest 10-pallet Matsuura MX-330, the current system had its limitations. So, after a fair bit of research, we concluded that hyperMILL fulfilled our needs better than any other system.”
The company that was founded in 1973 bought hyperMILL at the end of 2020 and the package is already making an impact. As Simon continues: “The cycle times and set up times are decreasing, especially as we always have our programming suites right next to the machines. We use our same top-end guys that do all the programming, setting and methodology of fixturing as well as running the machines. As the guys are all next to each other, all programming and fixturing can be done very quickly without having to go back to an office or acting as a liaison between people to undertake the tasks. As all the team see the projects through from start to finish, they are more invested in each job. This means that we always tend to get a better quality of product and a better understanding of how each part is being machined.”
Shearline Cell Leader and Programmer Mr Tom Biscoe says: “We have done a couple of jobs with hyperMILL and the difference shows. It just makes you quicker at doing everything. It is so much simpler to use, and a lot of the features are something that we didn’t have in our old software.”
“One of the big features that hyperMILL has that our existing software doesn’t, is the machine simulation. This undertakes the collision checking and also gives you a nice visual representation of how everything is going on the machine. This puts our mind at ease when we are watching something through, especially on 5-axis jobs that you know are going to be tight. If you see all of your holders and fixtures on the simulation and you know that nothing has gone wrong during simulation, it is down to us to ensure that nothing goes wrong on the machine.”
From a programming time reduction, Tom continues: “Having the ability to work off a single datum point, an impressive tool library and tool path flexibility has reduced programming times by 30% compared to our previous system. However, as we do a lot of batch work from 50 to 150-off that is often repeat orders, we will benefit from the programming efficiency going forward more than at present.”
One feature of hyperMILL that has impressed Shearline during the programming process is the tool library. As Tom says: “We did have a tool library on our old software, but because it wasn’t very good, nobody used it. With hyperMILL, the tool library is very helpful, especially with the fact that we have three machine tools with very large tool capacities. This means that we can use the same tool and spread it across all three machines and all of the functions remain and you can apply all sorts of cutting data to the tools and use that data for different tool paths.”
Concerning machining tight tolerance components, Tom says: “Another feature is the tolerancing on 3D tool paths. There is a tolerancing function that you can adjust, and this is a massive help to us; and as we see more of those complex parts that first enticed us to purchase the software, we are going to continually see more of those benefits.”
From a machining perspective, Tom enthuses: “We have reprogrammed some parts with hyperMILL and it is 10 times better than before. The cycle times on the machine are currently around 30% faster too. This is because there is no ‘air cutting’ like with the previous system. With our type of batch production and pallet loaded machines, this 30% saving will be significant. We are also witnessing far better surface finishes and tool life too.”
Alluding to the training from OPEN MIND, Tom Biscoe continues: “The training was really good considering the circumstances and the situation that we are all in at the minute with Covid. We’ve had two 3-day sessions so far and we have another one to go, but so far, we have got on very well with hyperMILL. I have been programming on our previous software for over 4 ½ years and I thought the transition was going to be difficult, but it hasn’t been. The other person that did the hyperMILL training with me, Harry, he’s only been here two years as an apprentice, so his programming experience is in its infancy, but he picked up the hyperMILL training really well.”
Confirming the ease of use, Shearline apprentice Harry Clark comments: “I have been on two 3-day courses, taking in part one and part two of the training. The first part was quite a steep learning curve as it was my first time using the software. By the second session, I had more time and felt more comfortable with the package, as I had a little time between the courses to use the software in a work environment. I am now looking forward to delving deeper into the full capabilities of hyperMILL and seeing what it can do.”
Harry continues: “I work on a 3-axis machine, but with the features of hyperMILL, I can now do so much more. hyperMILL has enabled me to work on fourth and fifth axis machines. The collision checking features in hyperMILL are robust and will do wonders for my confidence. The fact I can simulate the process beforehand is putting me at ease and giving me more confidence. One feature I’m looking forward to using more is the tool library. I feel like that will enable me to speed up my programming processes massively. Having all my tools saved in the system and ready to go would reduce programming times quite significantly. Previously, a lot of time could be spent setting up the tools and the tool paths, with hyperMILL you can configure a pre-set of how you like to have the tools in the tool path set up.”
Highlighting the advantages of hyperMILL, Simon Cooper says: “I think the real advantage is the ease of use and how the amount of effort required to make such top-quality components can be reduced. This enables us to have more people involved from further down the tier levels of programming experience. hyperMILL seems to have everything we could have wanted from a top-end system, and it is a proven product.”
From a capacity standpoint Simon concludes: “If you go to the trouble of investing in a £300k+ machine tool without having a programming suite to go with it, it’s a bad move. Now, we can not only offer our customers top-end machine tools, but also a top-end programming suite.”