Vertical Integration Powers Next-Day Precision Tooling
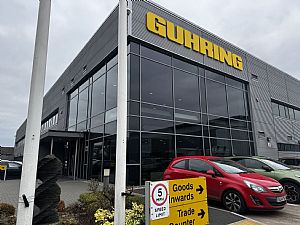
In an industry where precision and timely delivery are paramount, Guhring UK stands out as a manufacturing powerhouse. The company's Birmingham facility exemplifies a vertically integrated approach to cutting tool production that sets new standards for service, quality, and responsiveness in the precision cutting tool sector.
"We're very proud of the facility," explains Chris Bush, National Sales Manager of Guhring UK. "We've got Guhring-made machines to make our Guhring tools – this ensures quality, consistency and complete process control."
This single-site integration encompasses the entire manufacturing ecosystem, from raw materials to finished products. This stretches from production to coatings and regrinding services. The Birmingham facility houses not only standard manufacturing operations but also specialised tool production and coating capabilities that significantly extend tool life.
"We've got our own grinding machines. We've got our own coating facility," Chris elaborates.
"So once the customer has used our tools, they can come back here for regrinding. They're ground on the same machines that they're originally made on, coated with the same coating that they started with."
The facility's vertical integration model provides substantial benefits to customers throughout the product lifecycle. "You get the same performance from a regrind as you do from a new tool," Chris notes, highlighting a key differentiator in Guhring's service proposition.
When asked whether this comprehensive approach is standard in the industry, Chris is clear about their unique position: "We're unique in that. The size of the factory and the fact that we have everything you need, all in one place."
Unmatched Inventory and Rapid Availability
Perhaps most impressive is Guhring UK's commitment to product availability. "We hold so much stock here, we have £5m worth of stock on the shelf," Chris points out.
"I do think it's essential that we keep all this stock here within the UK," Chris emphasises. "We have 45,000 standard line items, and we’ve just released a new catalogue, another big book, bringing everything together in one book. We have extensive rows of stock readily available for next-day delivery or same-day collection."
This inventory strategy is specifically designed to address the unpredictable nature of manufacturing operations. "People can't plan for mishaps and breakages," explains Chris. "That's why we maintain a broad and readily available stock range. If someone needs something urgently, we can guarantee next-day delivery or even same-day collection."
This responsiveness is especially valuable in production environments where downtime incurs significant costs. By maintaining such a comprehensive local inventory, Guhring effectively serves as a strategic partner in its customers' operational continuity.
Engineering Expertise in the Field
Supporting this impressive manufacturing and inventory capability is Guhring UK's dedicated field engineering team. "Within the UK, we've got just under 100 people working for Guhring UK," Chris shares. "Of those, 22 are field engineers operating across the entire UK and Ireland."
These engineers act as technical consultants, delivering expert support directly at customer sites. "This allows them to visit customers and engineering firms, where they optimise cutting data, reduce cycle times, and ensure the right tools are selected for the right applications," Chris explains. "Ultimately, their role is to help make our customers more efficient and more profitable."
Coating Technology as Differentiator
A standout aspect of Guhring's technical capability is its in-house coating department. "It's all about time," Chris emphasises. "That's why we offer 10 different coatings here, and it's all application specific. So, depending on the application, we’ll have the right coating that goes on the tool for that process."
These specialized coatings provide significant performance enhancements: "With the coating, we can offer four times the tool life, from a bright tool to a coated one. And it's all under one roof."
By keeping coating operations in-house instead of outsourcing to third-party providers, Guhring ensures complete quality control throughout the manufacturing process. This integration also significantly reduces lead times, as tools do not have to leave the facility for coating.
Agility in a Changing Market
The manufacturing landscape continually evolves with new materials, tighter tolerances, and increasing production demands. When asked how Guhring addresses these changing market requirements, Chris points to the company's technical foundation: "Thanks to the facility we have and the expertise within our team, we're equipped to handle any demand that comes our way."
This confidence stems from Guhring's comprehensive approach that Chris succinctly summarises: "From the standards to the specials to the regrinds. Any application that comes our way, we've got the technology to handle it."
Industry Engagement
Guhring UK maintains an open-door policy for customers interested in experiencing their operations firsthand. "We have an open door policy, so any customers who want to come along and see it firsthand are more than welcome," Chris invites.
This transparency reflects the company's confidence in its operations and its willingness to demonstrate manufacturing capabilities directly to interested parties. It also underscores Guhring's collaborative approach to customer relationships, viewing technical partnerships as essential to mutual success.
In an era where global supply chains often separate manufacturing from end-users by thousands of miles and weeks of lead time, Guhring UK's Birmingham facility provides a compelling alternative. By combining extensive inventory, comprehensive manufacturing capabilities, specialised coating technology, and field engineering expertise in one location, the company offers a level of responsiveness and technical support that sets it apart.
For manufacturing operations across the UK and Ireland, this vertically integrated approach results in reduced downtime, optimised productivity, and a tooling partner with the technical ability to meet virtually any cutting tool requirement.