Voestalpine Invests in Edge Finishing Technology
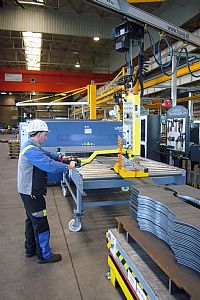
Processing over 60,000 tons of steel plate a year, Austrian manufacturer Voestalpine has invested in a slag removal, deburring and edge rounding system from Lissmac to increase production capacity and improve consistency. Available from Surtech in the UK, the new plant has been a revelation to the Linz based automotive manufacturer.
At the beginning of the steel plate production process at Voestalpine, the parts are cut by plasma or oxy fuel cutting machines. Whilst remarkably efficient and fast, this heavy duty cutting process is renowned for leaving large burrs, slag and oxidation on the edges of the plates that are cut.
Walter Radinger who is process manager at Voestalpine says: We process over 60,000 tons of steel plate each year for the automotive industry with components including structural parts and doors, bonnets, tail-gates and boot lids to name a few. What we needed was a process that was simple to set up and would provide the best available deburring quality. Additionally, we needed something that could deburr both sides of the steel plates in a single pass simultaneously. In addition to that, the machine would need to be energy efficient, low on maintenance costs and easy to maintain.
In the end we found that only Lissmac could fulfil all of our criteria. We were especially convinced by the performance of the slag removal machine. This was particularly the case when we cut thicker plates of 25mm and above where we historically have a lot of issues with large slag and burrs. Being convinced by the Lissmac machine, we immediately started looking at a second machine that could grind off the remaining burr and round off the edges. We again visited Lissmac Maschinenbau GmbH in Bad Wurzach Germany for a trial in their factory. The results were excellent and made it easy for us to order the second machine from Lissmac, says Walter Radinger.
Innovative slag removal
With parts that can weigh up to 35Kg each, it made perfect sense for Voestalpine to purchase a machine that could process parts in just one pass. By processing in one pass, productivity could be increased and the process could be made more ergonomic and efficient for the machine operators.
To this end, Voestalpine conducted numerous investigations and eventually selected the SBM-M 1500 D2 slag removal machine from Lissmac. This machine is connected in-line with a SMB-XL 1500 G2S2 de-burring and edge rounding machine to efficiently complete the whole process in one production cell. The steel plates are stacked on a pallet and then placed onto a lifting table in front of the slag removal machine. The table then raises to an ergonomic height for the operator who can then move the parts onto a roller conveyor. From here, they are pulled through the machine by drive rollers and conveyor belts.
During this first pass, the heavy slag is removed from top and bottom with hardened steel pins (power pins) mounted on two endless belts on the top and another two endless belts at the bottom. The process is simple and user friendly, as it allows the operator to set the through-feed speed and the material thickness of each individual job or batch of parts. Additionally, the top and bottom units can be adjusted independently for instances whereby the slag or burrs may be thicker on one face than the other.
Synchronised processing
According to Walter Radinger, Voestalpine run the two machine system in line. This ensures that parts go though the de-slagging machine and then carry on through the de-burring and the edge rounding machine all in one ergonomically flowing production cell. Despite this cell type of set-up, Voestalpine still have the flexibility of de-slagging or deburring only.
After the first process of de-slagging, the parts will go onto a roller table, which leads them into the SBM-XL 1500 G2S2 de-burring and edge rounding machine. With 8 heads used to deburr and round edges, the first four heads are equipped with abrasive belts that grind off upstanding burrs from the top and the bottom of the profiles. When they are free from burrs, the next four belts, which are equipped with abrasive flaps, will round off the edges on both sides simultaneously. The edge rounding belts run in both directions across the parts to make sure that all edges are finished in a uniform way. Depending on the weight of the parts, they are either hoisted by crane or hand onto a pallet for the next process.
High flexibility of the plate processing
The de-burring machine is easily adjustable through the user friendly touch screen control system. Normally, it is only necessary to adjust the material thickness and the processing speed. However, the Lissmac machine provides the opportunity to individually adjust the grinding heads or switch off any heads if they are not needed. The machines are just 1.4m and 2.1m long and can process parts that have a maximum thickness of 120mm. To further improve operator health and safety, the machines have a dust extraction system fully integrated to prevent any airborne particulate affecting the operators during the process.