Vollmer Cuts Cycle Times for Coventry Saw Blade Manufacturers KR Saws
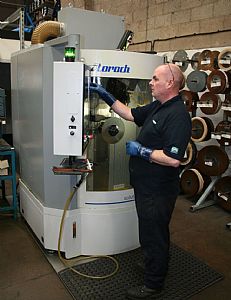
When KR Saws Ltd witnessed increasing customer demand for its circular saw blades, the company visited MACH 2010 where Vollmer UK provided the answer with its Loroch K850 Solution circular saw blade grinding centre.
Set up in 2004 as a joint venture by two of the world’s leading saw blade manufacturers, the Coventry based manufacturer of band saw and circular saw blades has witnessed continual growth since its inception. The growth is based on the strategy implemented by German and Dutch parent companies Roentgen and Kinkelder. The strategy enables both companies to respectively supply high quality band saw blades and circular saw blades to the UK, with KR Saws being the vehicle to provide bespoke solutions, specialised service and technical support from a UK base.
Previously operating four CNC profile grinding machines including an ageing Loroch CNC Turbo, KR Saws were witnessing a market place demanding increasingly sophisticated solutions. These challenges were compounded by the diminishing ability to meet capacity because blade production required secondary operations on additional machines.
The arrival of the 3-axis CNC Loroch Solution in September 2010 was the first Loroch K850 installation in the UK and it has proven a revelation to the Midlands based company. As KR Saws Managing Director, Paul Ison comments: “Our strategy of providing high quality products with unrivalled technical support and service is heavily dependent upon our production capabilities and capacity. The Loroch K850 acquisition has solved issues, improving our accuracy and repeatability and providing the technical team with the ability to offer a more diverse range of bespoke solutions.
Prior to the arrival of the Loroch K850, the company required two machines to produce a finished saw blade. Saw blades would be profile ground on one machine and then transferred to a second machine to complete the final bevelled top geometry. The Loroch K850 has immediately improved production cycle times and tooth geometry accuracy with its ability to grind the teeth and bevels in one set-up.
As Mr Ison continues: “We are manufacturing HSS, Carbide and Coated Carbide circular saws for steel, stainless steel and steel tube manufacturers as well as stockholders. With prestigious customers such as Tata, Caparo, Marcegaglia and Benteler among a few, we know that we have to continually evolve our products to deliver productivity gains for our end users. To this end, the 5-axis Loroch has a CAD facility on the machine that enables us to design any form or geometry at the machine. This allows us to offer solutions specific to each customer application to enhance their productivity.”
The Loroch K850 Solution also allows KR Saws to store the programs for its blade geometries on the machine. Programs can be efficiently changed from one job to the next. For customers acquiring batches of blades, the Loroch K850 delivers exceptional process repeatability and accuracy, guaranteeing grinding and tooth geometry accuracy.
Mr Ison continues: “The Loroch K850 Solution has been an exceptional asset for our business. It has been such a success that we have now ordered another machine from Vollmer, a Loroch KSC710 grinding centre. The new addition is due for delivery in July and is a fully automatic CNC grinding centre with an automated handling system for sharpening, re-toothing and chamfering our metal cutting circular saw blades.”
“Like the previous Loroch acquisition; we reviewed the marketplace and realised that there wasn’t anything else capable of meeting the productivity, accuracy or technical competence of Vollmer. The new machine is dedicated to automation with 3 saw blade stacks with a 230mm height. Two stacks can accommodate up to 40 blades each of varying diameter, tooth geometry, pitch and bore. Despite this potential culmination of blades, the machine will automatically generate the correct program for each blade as and when it is required. This will allow us to stack a machine in the evening with a variety of new blades or re-grinds and have the finished products ready for delivery the next day. Additionally, the new CNC acquisition will complete the blades with no requirement for secondary operations as it has a chip breaker grinding facility incorporated. This will further improve productivity, accuracy, repeatability and overall process control, giving our customers the benefit of continually receiving impeccable products,” concludes Mr Ison.