Vollmer Develops Tool Grinding in a New Dimension
2 July 2014
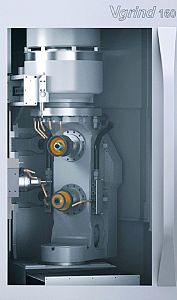
The launch of the new VGrind 160 grinding machine for solid carbide tools marks a paradigm shift for Vollmer, as it now enters the global market for processing solid carbide cutting tools.
As its first entry into the grinding of solid carbide cutting tools, Vollmer has approached the process from a radically new technological point of view. Unlike alternate machines, the new VGrind 160 utilises two vertical spindles to enable multi-level machining that is a first for machine tools of this type. This innovative new approach enables tool manufacturers to produce large numbers of solid carbide milling cutters and drills quickly and precisely.
Commenting upon the exciting new launch, Dr Stefan Brand, Managing Director of the Vollmer Group says: "With the VGrind 160, we are establishing ourselves in the international tool grinding market for the first time. For us, this is a logical and consistent step in order to develop our core competency in sharpening, and to further strengthen Vollmer's international position as a comprehensive solutions provider for tool production."
Using five CNC-controlled axes, the VGrind 160 grinding machine ensures precise machining of workpieces with remarkable precision and productivity. With the VGrind 160, tool manufacturers can produce solid carbide drills and milling cutters with diameters between 2 and 20mm. At the core of the VGrind 160 is the new kinematics system, which is controlled by two vertical spindles. The reasoning behind this is that unlike with a single spindle or horizontal double spindle, multi-level machining can be carried out thanks to the vertical arrangement. In addition, the spindle arrangement solves the common problems related to fixed and floating bearings, which leads to more precise results when machining workpieces.
Thanks to short linear axis travel distances and swivel ranges, the VGrind 160 enables customers to reduce machining times for machining workpieces. Non-productive times are shortened because tool manufacturers can load the two grinding spindles with different tools. An optional tool magazine with six grinding wheel packages enables tools on the vertical spindles to be changed over automatically. The pallet magazine for up to 550 workpieces, as well as further automation solutions, ensures optimal utilisation of the machine, around the clock.
The VGrind 160 achieves more precise results thanks to its multi-level machining, as a workpiece is only ever machined on the fixed bearing side of a grinding wheel set. Furthermore, the grinding wheel set is always located at the C-axis pivot point. This allows an accurate sharpening process beyond the realms of anything previously experienced. A further guarantee for precision and accuracy is the polymer concrete design of the machine. The solid foundation of the new VGrind provides improved damping and vibration behaviour whilst the design concept of the VGrind 160 leads to a compact and stiff construction with low space requirements.
To enhance user friendliness and ergonomics, the VGrind 160 can be easily and individually adjusted thanks to a height-adjustable, pivoting control panel. The display can be positioned to give the operator an optimal view of the graphic interface whilst the work area also remains visible. To control the VGrind 160, Vollmer uses the software NUMROTOplus. This system offers comprehensive applications for the production and re-sharpening of various tools. The software from the Swiss market leader, NUM, is used by over 40 different types of machine from 15 well-known manufacturers in 50 countries. This will create a familiarity and improved ease of use for customers.
"We developed the Vgrind 160 as an innovative platform, with which tool manufacturers can produce their products for their market precisely and efficiently. As a result, use of the VGrind 160 can be adapted extremely flexibly, both in terms of quality and quantities," adds Dr Stefan Brand.