Vollmer Leads the Way with First PCD Tool Production Event
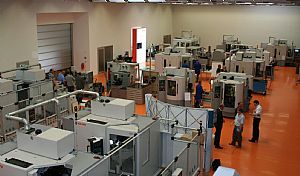
The recent PCD Days event at Vollmer's headquarters in Biberach, Germany proved a resounding success for the company and an extremely informative trip for the 30 UK customers who attended. The PCD event was aimed at giving customers a full insight into the technology and products available from companies with a wealth of experience in the production of PCD cutting tools.
The three day event commenced with presentations from Vollmer Werke’s Sales Director Jürgen Hauger and Vollmer UK's Managing Director Peter Allen.
The informative presentations provided customers with an insight into the company's products and ongoing developments. In conjunction with technology partners, the event met its goal of providing technological expertise that undoubtedly added knowledge and value for the visitors.
To complement the presentations, the visitors were given an extensive tour of Vollmer's manufacturing facility. The company tour not only provided visitors with an insight into what is behind the Vollmer name, it also gave an awareness of the ongoing research and development work that enables Vollmer to maintain its position as a world leader in the provision of machine tools for processing PCD cutting tools.
Vollmer Factory Tour & Technology
The tour of the 29,000sq/m plant commenced at the 'goods in' department. An area that instantly demonstrated how Vollmer implements flexible workflow systems throughout the entire business. At the centre of the goods-in area is an automated material racking system that holds over 800 bars, billets, tubes and strip materials that are continually flowing through the system to the respective production departments. With a machine tool lead time of six to eight weeks dependent upon machine model, the innovative workflow system is a critical element of the business.
To highlight the accuracy of the workflow system, Vollmer has an automated and 'live' storage facility that has over 80,000 stored components with 6000 part movements each day.
This finely tuned system enables Vollmer to supply its numerous production lines as well as end users demand for spare parts. This part storage facility includes the storage of parts for all machine tools dating back to the 1950's, regardless of whether the machine is still in production or now obsolete. As well as being a clear indicator of the precision logistics, accuracy and reliability of the system; it is a demonstration of Vollmer's service and supply commitment to its customer base. With over 30,000 machine parts and sub-assemblies that complete the existing 60 machine tools in the entire Vollmer range, logistics is as important an aspect to Vollmer as any other part of the business.
The thread of precision and automation was evident throughout the Vollmer production facility, as the 'live' storage facility not only provides spares and accessories to end users but also supplies the relevant production lines with JIT components for production. Billets and castings are transferred with pinpoint precision to the relevant machine tools as well as to a 160 pallet Fastems system that continuously feeds two Heller machining centres with a 400 tool carousel on each machine. This impressive level of automation and logistics is a critical cog in the company's quality procedures. By machining 90% of its parts in-house, Vollmer retains tight control over the quality of its parts and assemblies that complete each high quality machine tool.
Industry Leading R&D
With over 500 employees at its headquarters in Biberach, the UK visitors noted the high levels of automation and low staff levels in the production departments. However, as with any world leading manufacturer, the key to success is the evolution of new product development. At Vollmer there are over 80 staff employed in the R&D division with another department dedicated to prototype work to support the R&D work. The impressive R&D contingent is not only responsible for machine tool design, development, analysis, aesthetics and the incorporated technology but also the ExLevel software and control system that sets Vollmer apart from its competitors.
With almost 20% of the company's staff and 10% of its turnover re-invested in R&D, the company is conscious of its market leading position and is keen to remain the industry benchmark for developing new and innovative solutions.
Part of Vollmer's commitment to retaining its position as the industry leader, is its investment in 'the future' and its apprentice department. The company currently employs 64 apprentices that are the latest of 1100 trainees that have been employed by the company since the 1920's. The apprentices complete a foundation year in the dedicated apprentice department and from this point, their strongest competences are recognised and they are then trained in specific disciplines for eventual integration into one of the highly skilled teams involved in the development and production of the machine tools.
With a UK delegation that over the years has seen the demise of apprenticeships, it was clearly an eye opener to see a department dedicated to training teenagers for the future of the business and the wider manufacturing industry. However, in a German economy that boasts only 2% unemployment, recruiting apprentices in Germany is a competitive business for Vollmer as well as all other businesses, regardless of industry sector.
PCD Polishing Strategies
The informative factory tour was followed by a Vollmer presentation that highlighted PCD polishing applications and strategies. As part of the presentation, delegates were introduced to the technology and strategies of inserting, brazing and polishing PCD tips & chevrons into drill blanks. With the cost of a standard PCD drill ranging from £400 to £600, the presented strategies improve edge strength and geometries of a drill to improve tool life. Additionally, this evolution of the PCD drill enables the customer to have the drill re-ground 5 or 6 times - drastically reducing the overall cost of the drill.
New Product Developments
With such a depth of talent and ingenuity in its R&D and prototyping departments, Vollmer was keen to inform visitors of new developments that have been added to its existing machine tool range. The award winning QXD200 and QXD400 erosion and polishing machine tools have now received extended functionality for processing PCD drills with a high shear angle, whilst manufacturers of circular saws will be provided with added functionality for scoring saws.
For Vollmer's market leading QWD750 and QWD760 wire erosion machine tools, the R&D department has created a new start and stop function that is incorporated via the ExProg software. This feature enables the customer to interrupt the production cycle to make diameter and length corrections and then return to the same point in the cycle without returning to the start of the cycle, thus saving considerable production time.
The market leading QXD machine has been a major success for Vollmer since its market introduction in 2009. For visitors working with the QM machine, the predecessor of the QXD, the QXD undoubtedly aroused interest. When Mr Arndt Hauger, Vollmer's PCD Product Manager was asked how much more productive the QXD is, in comparison to its predecessor, Mr Hauger made an eyebrow raising point that the new QXD is at least 2.5 times faster than the QM machine of four years ago. With ongoing developments to the ExLevel software, this gulf in technology will continue to grow; not only between previous machines but also machine tools developed by Vollmer competitors.
With improved motion systems, automation systems and software strategies, Vollmer estimates that erosion with the QXD is now at least 30% faster than grinding. This exponential progress highlights how fast the company is moving and how the family owned business has developed since being an ammunition manufacturer during the 2nd World War.
Collaborative Partners
Whilst the processing of PCD tooling clearly evolves around the machine tool and technology employed, as a 'PCD Event' Vollmer was intent on involving partner companies in the event to provide visitors with an overall insight into the production, processes and technology involved with PCD cutting tools. With longstanding international relationships with manufacturers throughout the PCD processing chain, presentations were also delivered by technology partners Alicona, Haimer, Gerling, Element 6 and Zoller to provide a complete overview, giving the visitors relevant information for the entire PCD production process chain and not just the Vollmer erosion technologies.
As a provider of optical 3D measurement systems in high resolution, Alicona measurement devices are used as tool measurement devices for cutting edge measurement, as roughness and form measurement devices. The Focus-Variation technique of its Infinite-Focus product line combines traditional surface metrology and micro coordinate measurement technology. Presented as a complementary technology to Vollmer, visitors were given an insight into the benefits of analysing PCD tooling with such systems.
The Alicona presentation was supported by a discussion from Haimer. Claiming to be the European market leader in the production of toolholders with daily production of over 2000 units, Haimer informed the visitors of the range of products available before giving a shop floor demonstration of its vertical tool balancing equipment. Suitable for the balancing of PCD tooling, grinding wheels and the automatic balancing of arbors, the Haimer range proved of extreme interest to the UK visitors.
Complementing the Haimer balancing and toolholders was a presentation from Zoller, demonstrating its fully automatic measuring machines for cutting tools that enable the end user to measure and check tools without any specialist knowledge. With systems for tool pre-setting, inspection and measuring as well as offering a tool management system, Vollmer UK's customers were intrigued by the possibilities and cost saving potential of these systems. It was this registered interest that justified the signing of a distribution partnership between Zoller and Vollmer UK.
Commenting upon signing an agreement in Biberach, Vollmer UK's Peter Allen comments: "At Vollmer UK we are intent upon providing our customers with the most technologically advanced, productive and cost effective solutions that have unsurpassed quality and service as a given. Whilst we can offer machine tools and services, there are peripheral products beyond our scope that are complementary to our range. With its outstanding reputation and ability to support our customers with products beyond our portfolio, I feel that Zoller is an ideal fit for our business and customers will undoubtedly benefit from the agreement as we move forward."
Further presentations from Gerling and Element 6 were more focused on the brazing and composition of PCD. The Gerling presentation highlighted how its products can improve product consistency and quality by fully automating the brazing process. The Gerling discussions revolved around the cleaning, positioning, temperature control, soldering and efficiency of automating the brazing process. Upstream from all these complementary innovations was the presentation from Element 6. As a subsidiary of the DeBeers Group that is moving its R&D and manufacturing facility from Ireland to Oxfordshire in Q1 of 2013 with a £20m investment, Element 6 highlighted the PCD and PCBN materials that it manufactures and the benefits and uses of the grades.
For manufacturers of PCD tooling this was an insight into the numerous grades available and the applications of each grade.
Whilst Vollmer has very close association with its technology partners internationally, Vollmer UK will be aiming to further develop its relationships with the respective companies to ensure that its UK customer base are fully informed and employing the technologies and philosophies that will enable customers to supply cutting tools beyond the productivity and capabilities of their competitors. This close collaboration proved a resounding success in Biberach with customers being well educated with regard to the entire PCD production process. With such positive customer feedback from the trip, providing this knowledge and technology transfer to the UK PCD industry, will benefit Vollmer, its technology partners and most importantly the end users.