Vollmer Sparks Success for Tooling Manufacturer
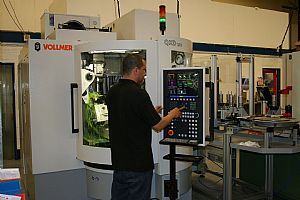
When Exactaform realised that its CBN insert production could not compete with cheap Asian imports from multi-national manufacturers, it made the bold move to target niche markets with rotary diamond tooling. And nine years after the company acquired the UK’s first Vollmer QWD760 5-axis wire erosion machine for the automatic measuring and erosion of tools – the company has grown to become the UK’s largest independent PCD tooling manufacturer.
When Asian and eventually global OEMs drove the price of CBN inserts from approximately £50 down to £15-20 over ten years ago, the small Coventry based tooling manufacturer had to evolve to survive. The strategy of diversifying into rotary PCD & PCBN tooling has paid dividends for Exactaform. Since acquiring its first manual Vollmer QWD760 for finishing the profiles on its cutting tools, the company has since purchased an additional five Vollmer machines with another currently on order. This has enabled the strategy of diversification to thrive. The company doubled its factory space to 10,000sq/ft in January 2010 and has continually posted annual growth figures of 25-30%.
As the company has developed its expertise and products, the customer base has developed to encompass military, aerospace, F1, automotive and the general subcontract market. Primarily supplying bespoke tooling solutions for a wide customer base has been a challenge that Exactaform relishes, as General Manager, Mr Peter Raynor comments: “Our continued commitment to investing in technology and staff combined with the ability of Vollmer to provide the right machine tool solution, are the primary reasons for our remarkable success.”
“Our first Vollmer QWD760 is a manual machine than requires operator intervention, so it runs for 40 hours a week. However, as the business has grown we since acquired an additional three QWD750H wire erosion machines with robotic loading to automate the process.”
The latest QWD750H arrived in January 2010 and the three machines each have a 12 station carousel that enables Exactaform to run the machines unmanned. With each cutter taking anything from 45 minutes to 3 hours to machine, depending upon the cutter geometries, Exactaform can set the machines to run unmanned overnight. As Mr Raynor continues: “The labour intensive aspect for us is tool building. We have 18 employees and most are building tools with only two operators running the 6 Vollmer machines. The QWD’s run an average of 120 hours a week, every week. When busy, we have run the Vollmer’s for 160 hours out of a possible 168 hours in the week, with the remaining 8 hours used for wire changeovers.”
When specifying its machines, the choice is simple for the ISO: 9002 company, as Mr Raynor states: “When we bought our first Vollmer there genuinely wasn’t anything else available on the market. Now, alternate manufacturers are trying to offer solutions, but they are nowhere near the quality, capability, specification or performance levels of the Vollmer’s. The competitors are offering technology that is ten years behind Vollmer.”
Despite giving Exactaform staggering levels of automation, a key benefit to the company is the flexibility of the wire erosion machines. All the QWD machines have access to a central server that stores a history of thousands of tool programs. From this database, the machine operator can download the 12 required tool programs and select the order of the tools to be machined. This flexibility allows Exactaform to meet the rapid turnaround times of its F1 customers whilst enabling the company to offer end users an equally low price for one-off tools as for tools in a batch run. It also allows Exactaform to turn tools around within 24 hours for customers with urgent requests.
Further enhancing the automation and productivity is the probe system that automatically measures and orientates the tool to compensate for a tip that has been brazed out of position. This reduces manual setting whilst ensuring the desired dimensions are achieved to within a tolerance of 0.001mm with repeatability within 5 microns for a batch of 12 tools. Despite the exceptional productivity levels of the Vollmer QWD machines, the growth at Exactaform has required additional machines.
As Mr Raynor comments: “Three years ago we realised we had to step our production levels up to meet customers rapidly increasing demands. Vollmer once again had the solution with its QXD200 rotary erosion machine. Whereas the QWD machines would have the same cycle time regardless of whether they were removing 2 or 10mm, the QXD is specifically for removing small quantities of material at higher speeds.”
The QXD200, acquired in 2009 accommodates 12 cutting tools and up to 6 wheels. At Exactaform, the individual wheels are used for gashing operations and OD grinding with large wheels used for roughing and smaller wheels for finishing. The QXD200 has proven 20 to 30% faster than the QWD machines at Exactaform. However, this is only applicable to nominal material removal rates. The 6 simultaneously controlled axes and ability to measure, erode, grind and polish has been complemented by new Vollmer software that enables Exactaform to complete cutting tools on the QXD200 machines in one set-up. Like the QWD machines, the QXD is highly automated to improve cycle times and process capability. This ream of benefits noted the company taking delivery of a second QXD200 in January 2011 with another on order. The second QXD has a 29 tool changer, more than its predecessor.
The probing system on the QXD200 not only measures and orientates the tool but also probes the wheels. This calibration corresponds with an automatic wheel dressing cycle that communicates any wheel deviations to the CNC for automatic path compensation.
Discussing the levels of automation at Exactaform; Mr Raynor states: “The machines have a traffic light system, a wireless sender and a camera network. This enables us to remotely receive emails with video footage that informs us how many jobs are left in production or alternately if a machine goes down. This ensures that a machine is never down for any lengthy period of time.”
“With regards to the generating of programs, Vollmer has developed software that rapidly enables us to generate a Vollmer programs directly from a DXF file. This innovative system saves us significant time in the office and on the shopfloor. It is evidently clear that Vollmer has gone from strength to strength by paying considerable attention to the finite details of its machine tools and this has in turn enabled us to be the industry benchmark in PCD tooling. We are delighted with Vollmer and they have played a major part in the success at Exactaform,” concludes Mr Raynor.