Vollmer Supports Growth for Scottish Saw Blade Manufacturer
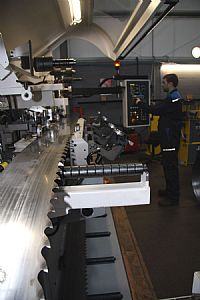
With the provision of saw blade manufacture and service for the woodworking industry being a competitive industry, EPS Services & Tooling has always strived to stay ahead of its competitors. In its latest drive to stay ahead of its rivals, the company with manufacturing sites in Wiveliscombe, Devon and Kirkcaldy, Fife has installed a Vollmer RC110 automatic levelling and tensioning machine for processing its bandsaw blades.
As an existing Vollmer customer with six machines at its Kirkcaldy site and another 10 Vollmer machines at its primary production facility in Devon, the investment in the RC110 was made to improve the quality and consistency of its bandsaw blade production and most importantly, increase the company's capacity levels.
EPS Services & Tooling, Managing Director, Mr Nick Palmer discusses the investment in the Scottish facility: "With a number of competitors around the UK, we have strategically located our business to service the South West and Wales since the company's inception almost 40 years ago. Just over five years ago we had the opportunity to enter the marketplace in Scotland and we took it, as it enables us to be close to our customers and offer a local level of service beyond our competitors. This strategic move has paid dividends as our business has grown considerably in the region. This growth is credit to our investment levels that have seen us install the first Vollmer RC110 in Scotland."
As a manufacturer of wide and narrow band saws with the ability to sharpen and re-stellite tip, as well as TCT circular saws, edger and canter rings up to 1.2m diameter, also sharpen HSS and carbide planing knives, chipper, guillotine and shear blades along with other various woodworking tools.
EPS has invested heavily in the latest machine technology to guarantee the production quality and consistency that customers demand. As Mr Palmer continues: "The investment in the Vollmer is to aid our business on a number of fronts. Firstly, Saw Doctors are a dying breed and whilst we have employed 5 new apprentices across our two sites and are proud to be in the minority as a company training Saw Doctors, we have to automate more of the business to maintain pace with demand. Secondly, as the cost of production increases, there is a price pressure on manufacturers to automate the production of saw blades."
"From an end user perspective, the demand for improved running times is forever increasing. To this end, our quality and consistency has to be of the highest standards to ensure we retain the confidence of our customers. Additionally, as the expectation for improving quality and up-time is relentless, more wood mills are outsourcing their tool sharpening to companies like us; as we are prepared to invest in the machinery to guarantee the wood mills achieve their production targets."
With regard to the Vollmer RC110, since its installation in January 2013, the new investment is already paying dividends.
Originally the saw doctors at the Kirkcaldy plant manually levelled and tensioned each band saw blade. Now, they can set up the RC110 and allow the machine to automatically process bandsaw blades whilst simultaneously continuing to manually tension blades where needed. The benefit to EPS is that its capacity levels have instantly increased with output now extending from 200 to over 300 blades each week in Kirkcaldy. The level of automation has simplified the production process for EPS whilst freeing up the time of the highly skilled saw doctors. For EPS, this means one thing, an opportunity to train new staff. As Mr Palmer continues: "Our saw doctors have always dedicated their time to meeting our production demands, now the RC110 affords our highly skilled staff more time. So, rather than de-skilling a dying trade, we are employing apprentices. The apprentices can learn how to use the RC110 to gain experience of the latest CNC machining techniques and when the machine is set and running, our saw doctors can train the apprentices in the art of levelling and tensioning saw blades manually."
From a consistency standpoint, the RC110 eliminates operator error and it guarantees continuity of supply in the circumstances of highly skilled personnel being unavailable for work or on holidays, also allowing greater flexibility within the staff.
Commenting upon the reason behind acquiring a Vollmer machine, Mr Palmer continues: "We have two machine shops that are full of Vollmer machine tools. They are extremely reliable, highly productive and very well supported by Vollmer. The build quality and technical ability of the machines is far beyond that of alternate machines. Furthermore, we already have a Vollmer RC100 at our Devon facility, so we knew that its replacement, the new RC110 would provide familiarity, continuity and above all confidence from the performance and service support that we already receive from Vollmer."
Proving the reliability of Vollmer machines, in October 2011 the company also installed a CA200 automatic profile grinding machine at our Fife facility, capable of processing bandsaw blades up to 270mm wide. A second CA200 machine followed 12 months later. The first CA200 CNC controlled machine with limitless grinding profile programs and automatic wheel dressing was acquired as a result of a new service contract that EPS had won with a sawmill.
Grinding upwards of 60 blades each week with impeccable precision and reliability, a second machine soon followed. The second CA200 machine was installed to replace an existing machine with reliability issues. The previous machine was unreliable and this was unacceptable for a machine shop with a high blade output. As the first Vollmer CA200 proved itself from a reliability, precision, quality and user friendly perspective - EPS looked no further than Vollmer for the second machine.
In fact, the acquisition of the Vollmer RC110 has gone beyond the realms of expectation for EPS Service & Tooling. Only launched in August 2011, the new RC110 incorporates a new curved door design that gives the operator improved access to the work envelope whilst a new measuring unit has significantly improved accuracy over its RC100 predecessor. Further innovations that are new to the Vollmer RC110 are an improved tensioning lift system that uses twin roller bearings for alignment rather than a single roller system on the RC100 machine. This simplifies the tensioning process for the machine operator whilst improving the overall accuracy. The CNC software has also witnessed an upgrade. Whilst the operator interface provides the same procedures and appears identical, the Vollmer team has incorporated incremental changes to improve the user friendliness whilst delivering shorter programming and overall processing times.
These improvements haven't gone unnoticed by EPS, as Mr Palmer concludes: "The new Vollmer RC110 has been a great purchase for us. In the short time since its installation it has already exceeded our expectations and we can clearly see the benefits of the RC110 versus the RC100 machine. It has improved our productivity, capacity levels, quality and the consistency of that quality as well as enabling us to free up highly skilled staff to train new apprentices. The investment also demonstrates our commitment to the Scottish marketplace and our dedication to continually improving our quality, service and support to our growing customer base. With plans afoot to move to larger premises and employ more staff in Scotland in the next three years, we are confident that Vollmer will play an integral part in our growth strategy."