West Wales Company is a Trailblazer With New Kerf Machine
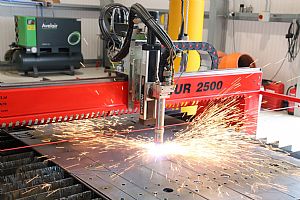
Founded over 30 years ago in a small ‘shed’, CLH Trailers has grown into one of the UK’s leading manufacturers of trailers for the agricultural, fishing, marine, sport, leisure and farming industries. As the product range has grown, so has the factory, staff levels and investment in technology – with the latest addition to the plant list being a plasma cutting machine from Rochdale manufacturer Kerf Developments.
Located in the picturesque village of Saint Clears, between Camarthen and West Wales holiday hotspot Tenby, the 15 employee business manufactures hundreds of trailers every year; and with anything from 50 to 200+ components in each trailer, productivity and precision are critical for CLH Trailers. With a burning desire to keep moving the business forward, Managing Director Mr Chris Hussell and shop floor foreman of over 20 years, Mark Reynolds started looking at available options for cost savings and productivity enhancements.
Taking up the story, Mr Reynolds says: “First and foremost, we wanted to buy British. We looked for a viable option and we realised that laser cutting wasn’t suited to our business whereas plasma was a perfect fit. We found several vendors and we then spoke with customers for their testimonials. Out of the UK manufacturers, it was Kerf that had a reputation above all others. This reputation was backed by their customer approach and of course, the quality and productivity of their demonstrations. We were about to purchase a RUR 2500p plasma machine with a 4 by 2m bed – and then the pandemic hit. We initially put the order on hold, but as the lockdown continued and we retained a steady level of business, we realised that the potential benefits of the Kerf plasma would send our business on a forward trajectory, so we finalised the order during the pandemic and the machine was delivered in July.”
Primarily cutting black steel and aluminium in thicknesses from 1.5mm to 25mm, CLH Trailers specified the RUR2500p machine with the user friendly Burny 10 LCD CNC controller, the powerful 275amp Lincoln Spirit II 275 plasma unit and Lantek software to drive the high-definition Ultrasharp cutting technology. Building a new factory unit specifically for the new Kerf machine, Managing Director, Chris Hussell says: “I wanted a machine with a robust build quality that is capable of running all day, every day. The Kerf machine certainly gives us that. The plasma unit can cut steel beyond 60mm thick, which is more than we need and the precision, repeatability and edge finishes are exceptional. We predict that the machine will pay for itself in less than 2 years.”
Creating Savings Everywhere
Looking closer at how the new Kerf plasma will create such significant savings, Mr Reynolds continues: “As a business, we typically have 6 staff manufacturing parts to complete an average throughput of two trailers each day. The majority of parts require guillotining, notching, drilling, grinding, corner rounding, bending and welding before galvanising. Each of these processes can be slow and labour intensive; and with each subsequent operation, there is an increased opportunity for error and potential scrappage. With the Kerf machine, we can do many of these operations in a single set-up. Going forward, this will free-up at least two employees for other tasks. A labour saving of at least £40k is great; but equally important for a company in a rural area is that the plasma allows us to grow the business whilst re-distributing the highly skilled staff we have.”
Providing a practical example of savings, the mudguards on each trailer are processed in quantities of 6 to 8 from an 8 by 4ft sheet of 1.5mm thick black steel. “The batch of mudguards would take 10 minutes to cut on a guillotine, then another 10 minutes on our variable angle notching machine followed by another 10 minutes for marking and subsequent drilling with the final process before bending being the grinding and rounding of the corners, which takes another 5 minutes. If you add to this total of 35 minutes additional time to move the mudguards from machine to machine and position the parts in jigs, you’re looking at over 40 minutes. The Kerf plasma will profile and cut the holes in less than 10 minutes with far superior precision. Not only does the Kerf machine reduce our cycle times by more than 75%, but it also removes the opportunity for operator error, improves quality and consistency, eliminates hand finishing and frees-up capacity from existing machines.”
“We’ve only had the Kerf machine a matter of weeks and it has already lightened the workload of our staff and our machines, streamlining our production. Our guillotine was working for over 4 hours a day, now it's only used for an hour a day.”
Design for Life
Manufacturing ATV, livestock, flatbed, beavertail, container, motorbike, boat, tipper, tilt-bed, signage, car transporter and camping trailers to name a few, each design can have beyond 200 components. At present, the Kerf high-definition plasma is only cutting 15-20 different components, something that will rapidly change, as Mark states: “Our designs and aesthetics were limited by our machine capabilities and also a limited appetite for innovative designs from the ‘function-first’ approach of the agricultural sector. The Kerf machine opens up a world of opportunity to re-design trailers for improved aesthetics, functionality, light-weighting and even the potential for reduced components and shorter assembly times. The mudguards are one component that we have already re-designed to improve the aesthetics, reduce material usage and weight, and also offer a wider range of shapes and sizes. This is the first demonstration of how we can move our designs forward to create a greater appeal among the consumer market.”
Another example of design for manufacture and aesthetics is the winch post for boat trailers. Previously manufactured from three pieces of 5mm thick steel that are each cut to size, punched, notched and then jigged for welding; each winch post takes 30 minutes to produce – a time only achieved when efficiently processing in batches of 20+. “The capabilities of the Kerf machine have allowed us to redesign the winch posts and these are now profiled with holes in less than 2 minutes with an additional minute for second-op bending,” continues Mark.
“We have also re-designed the hinge assemblies for loading gates on agricultural trailers. We produce over 40 of these thin long parts every month and they were cut and punched before welding two gudgeon pins to each hinge. The gudgeon pins were made externally, so by re-designing the hinge assemblies we have eliminated the requirement, cost and lead time of the gudgeon pins. Most importantly, the cycle time has been cut from six minutes per part to 30 seconds. The hinges are a perfect example of how the capabilities and precision of the Kerf machine has enabled us to redesign an existing part to eliminate subcontract costs, reduce cycle times, reduce material requirements and reduce the weight of the part. Additionally, I can set the RUR2500p to cut 40 hinges and leave the machine running to do other tasks. Essentially, the Kerf machine is giving me more time to be productive elsewhere and even look at other opportunities for the business.”
Kerf Creates Opportunities
Looking to the future, CLH Trailers Managing Director, Chris says: “We have always undertaken an element of subcontract metalworking and fabrication, but now we can extend this significantly. The Kerf machine has only been here a short while and we are already doing decorative wrought iron fencing, cutting letters and signage and much more. The potential of the Kerf machine is huge. Equally significant are the savings. On top of the labour and cycle time savings, the reduced waste and added capacity throughout our facility has been hugely noticeable in a short period. But, one of the biggest savings for us will be on the material. We order 6 tonnes of sheet steel every month and an additional 4-5 tonnes of box section, up to 30% of this is wasted in off-cuts that are sent back for recycling.”
“With the Kerf plasma we have already taken our material utilisation from 70% to 85% and the more familiar we become with the machine, the more material and costs we will save. This is a credit to the Lantek software and Ultrasharp cutting technology that nests the parts in very close proximity to minimise waste. Furthermore, we can use off-cuts from larger parts to nest and produce small batches of smaller parts such as brackets, making sure we waste minimal amounts of material. With thanks to Kerf, we are very excited about the future of our business. It is great to see two UK manufacturers supporting each other, developing relationships and successfully rising to the challenge of the current economic climate,” concludes Chris.