Westwind Reduces Subcontract Costs With Tornos Investment
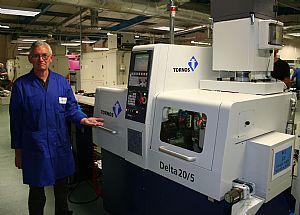
As the world's leading and largest specialist designer and manufacturer of air bearing spindles, Westwind Air Bearings is enjoying significant growth levels across many of its spindle sectors. To support this growth, Westwind has undertaken an investment program to bring the production of jets, and a number of additional small machined parts in-house from subcontractors.
The reasoning behind bringing the work in-house was to reduce subcontracting costs, control its own destiny with regard to lead times and batch quantities whilst avoiding the financial penalties of continually changing batch runs to meet its Kanban schedules. To achieve all this, Poole based Westwind acquired a Tornos Delta 20/5 and a Tornos Deco 10A.
With the production of 30,000 jets per week being subbed out, Westwind required sliding head lathes that could offer high levels of productivity, unmanned running and flexibility. The company reviewed the available vendors and selected the Tornos Deco 10A. With four existing Tornos Deco 20’s that had been running for over 13 years, Westwind Air Bearings was familiar with the reliability, machine build quality and service support that Tornos is renowned for.
Since the arrival of the Deco 10A in February 2012, it has been running 24/7 to produce 20,000 thrust and journal jets a week, as well as running development batches for new spindle designs. As Westwind’s Manufacturing Engineer, Mr Steve Somers comments: “The Deco 10A is running 24 hours a day. We are so confident in the uptime and its ability to retain tolerances that we only conduct twice daily inspections on a two-day product run. Despite being a production machine, we run batches from as small as 50off up to 100,000 on the Deco10A, so a combination of flexibility and productivity is critical.”
With a 3m barfeed, the 2mm diameter brass jets have the OD turned, faced and drilled on the main spindle whilst the sub-spindle simultaneously turns, drills and uses a form tool to complete each jet in 20 seconds. The three jets per minute productivity is credit to simultaneous front and back end working as well as the use of a high frequency 20,000 spindle for drilling the micro holes through the brass jets.
As Mr Somers recalls: “Our productivity rates enable us to comfortably satisfy our Kanban schedules as well as produce for stock without the cost, confidence or product control issues created from subcontracting the work out. Our quality and tolerance bands are very tight. We have 23 different types of jet running on the Deco10A and the maximum set-up time for each job is never more than 5-10 minutes. This is because we have a top and bottom tooling platen that are optimised with the top platen consisting of turning, boring and spot drilling tools and the bottom platen holding parting, turning, drilling and spotting tools. With an optimised configuration, we have a production machine with outstanding flexibility.”
Producing specialist spindles for processing Printed Circuit Boards (PCBs) with rotational speeds from up to 350,000rpm, high-precision linear and rotating equipment for the semi-conductor processing industry, spray paint spindles and additional high end spindles, Westwind is continually evolving and developing its product range. To support this, the company invested in the Tornos Delta 20/5.
As Mr Somers continues: “We bought the Delta 20/5 to produce small intricate parts such as screws, rivets, restrictors and other spindle parts that are small production runs or development batches that were previously modified externally. By bringing this work in-house, we have full control over the development and testing of parts for new spindles without the involvement of subcontractors.”
“The Delta 20/5 gives us full process control over all the specialised parts we now manufacture internally. The set-up time can be up to 30 minutes compared to 5 minutes on the Deco, however this takes into account collet and tooling changes that are required for processing bar from 2 to 16mm diameter from a diverse range of materials that include brass, stainless steel, monel and aluminium alloys. The Delta now has over 50 different types of job regularly produced and this is constantly growing, which is testament to the flexibility of the machine,” says Mr Somers.
With over 60 staff on the shop floor, the Dorset manufacturer conducts production as well as R&D work whilst the company’s second manufacturing facility in China is a volume manufacturer.
“The new machines have saved us considerable sums in subcontracting fees, reduced our lead-times and improved the through-flow of work. Furthermore, we are in full control of our production and development work. From a production perspective, the Tornos machines support our Kanban system and from a development viewpoint, we have streamlined the process from drawing office to finished part. Our 13 year old Deco is extremely capable and productive and I have little doubt that the machines we have just purchased will serve us just as well,” concludes Mr Somers.