World's Longest Established EDM Manufacturer Keeps the Innovations Coming
27 March 2015
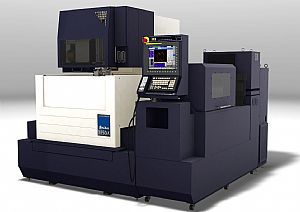
As a company that claims to have made the worlds' first Wire EDM machine in 1972, Seibu has a rich and established reputation in the EDM marketplace. To further establish its reputation, the latest addition to the Seibu line is the M50A is available in the UK from CNC International.
The new MA series of Seibu EDM machines are packed with innovations that create a platform that will reduce energy consumption, improve productivity, service life and operator ease-of-use. The M50A is a high speed, high precision and extremely functional machine that is demonstrated by its pitch cutting accuracy of +/-3microns and wire diameter capacity from 0.1 to 0.3mm.
Sitting between the smaller M35A and the larger M75A machines, the M50A provides an ideal working envelope of 800 by 650 by 300mm (WxDxH) with a maximum workpiece payload of 800kg; a dimensional range that accommodates most machine shops. This spacious work area sits within a compact 2235 by 2400 by 2070mm (WxDxH) footprint that is considerably smaller than competitor machines. This footprint is upward of 35% less than alternate machines, which is credit to the vertical sliding door for the work tank, which also improves operability as well as slashing the floor space requirement.
From a technology standpoint, CNC International has over 25 years in the EDM market, so when it decided to team up with Seibu, it was because of the advanced technology within the Seibu range of machines. Some of the features that appear as optional extras on the new M50A include a Core Stitch function. This means the de-tagging or parting off process is no longer necessary. Instead of leaving a tag, the Seibu, using the brass wire, welds the core in place as it is cutting, so the operator only has to tap the core to remove it. The benefits of this unique system include a reduction of man hours and error prevention. It also simplifies the NC program, as programming for uncut parts is eliminated. The impressive core stitch feature typically reduces cutting-off core times by over 95% whilst improving efficiency by over 50%.
EL Coating is another new technology on the Seibu line. It prevents cobalt (Co) from dissolving in water by means of coating the cutting surface with brass. Anyone familiar with EDM processes understands that when tungsten carbide is cut in water, the cobalt (binder) starts to dissolve in water and as a result, the material becomes weak. The EL coating system from Seibu makes it possible to cut in water, which makes maintenance work very easy. The new system makes it possible to cut in water by coating the cutting surface with brass. This also enables customers to obtain far better results with the use of an anti-corrosion material.
Another innovation available on the Seibu M50A is the Thermal Adjust 24 feature. This feature maintains the vertical positioning of the wire by correcting the thermal displacement that is caused by the temperature change between the upper and lower heads on an EDM machine. In the case of extended cutting times, the vertical position of the wire can't be maintained because of the thermal displacement between heads as well as potential ambient temperature changes. This impressive new system guarantees the verticality of the wire can be improved beyond 60% compared with alternate EDM machines.
A key feature that will appeal to anyone involved in EDM is the Automatic Wire Feeding (AWF) device on the Seibu M50A. The Seibu has a number of quirky innovations that combine to improve this feature greatly. These include the continuous passing of an annealing current through the wire to keep it straight and enhance the feeding process. The M50A also has a round diamond die guide that improves precision whilst a jet feed guide flushes water from the upper nozzle to improve the feed rates. For further details on how the impressive Seibu line of EDM machines can improve the productivity of your shop floor, please contact CNC International.